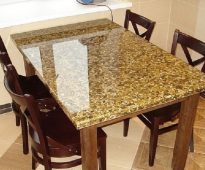
We make a manicure table with your own hands
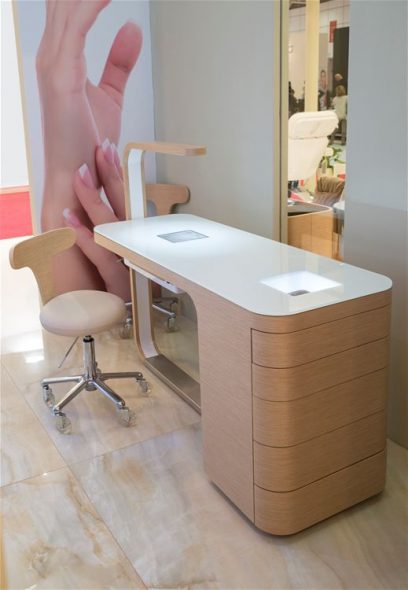
Beautiful manicure table for the master of nail service
The main workplace of the master of nail service is a manicure table. This item becomes an integral part when you take your clients in the salon or at home. It is on the professional desk that you can install special equipment that will allow you to collect nail cuts.
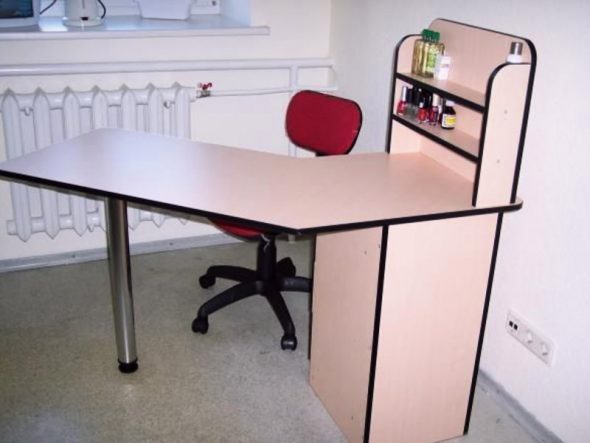
Comfortable table and easy chair for the manicurist
However, this item can be used not only for its intended purpose, this inventory can be used for procedures related to cosmetics. Faced with the need to purchase professional equipment, it becomes clear that in specialized stores it has a very high price and may not be suitable in size.
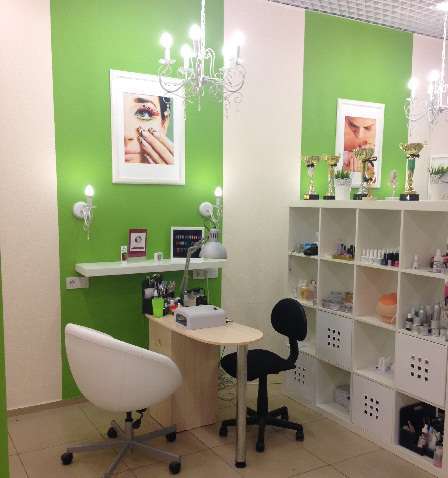
A small manicure table in the interior of the manicurist’s office
Do not be upset, there is a very simple way out. Make a manicure table with your own hands.
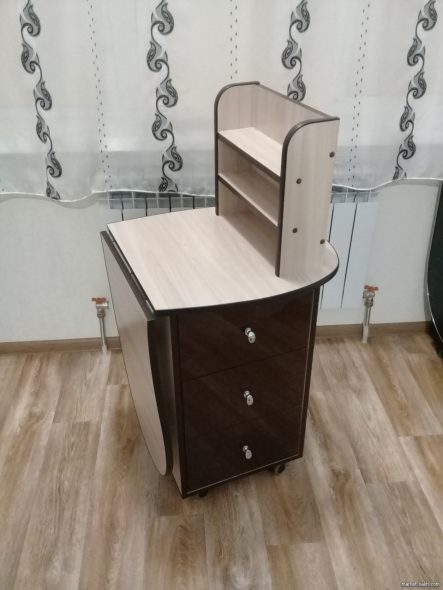
Folding manicure table with shelves takes up little space and turns into a workplace at the right time.
Now let's talk in more detail about what it consists of.
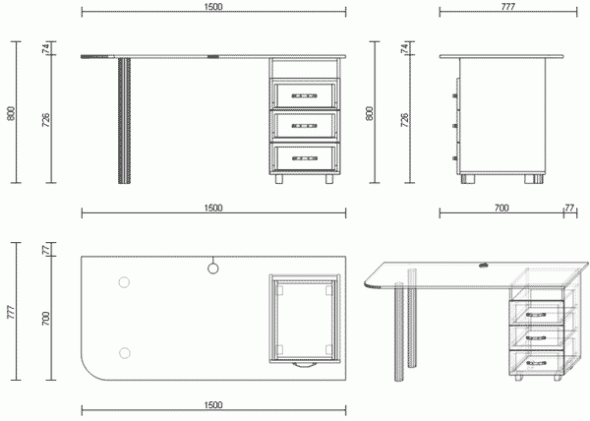
Detailed drawing of a manicure table with drawers with dimensions
Content
The design of the manicure table
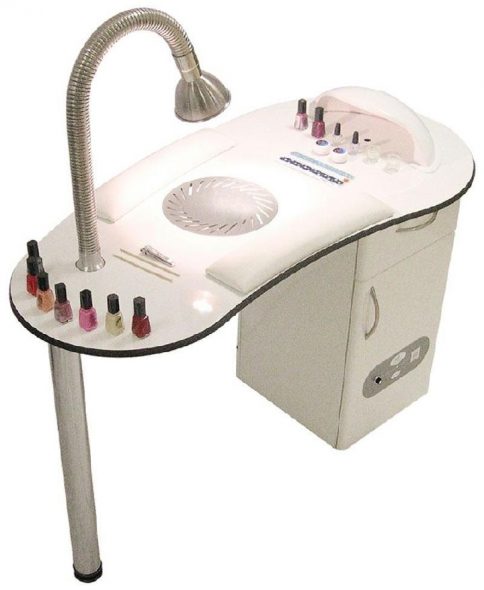
Manicure table: convenience, functionality and attractive design
From the table top, drawers with drawers and supporting legs consists of any professional equipment. In the manufacture should take into account that the size of the working surface of the table should correspond to the possibility of landing behind him two people. On the one hand, the table must have a cabinet with drawers or regular shelves.
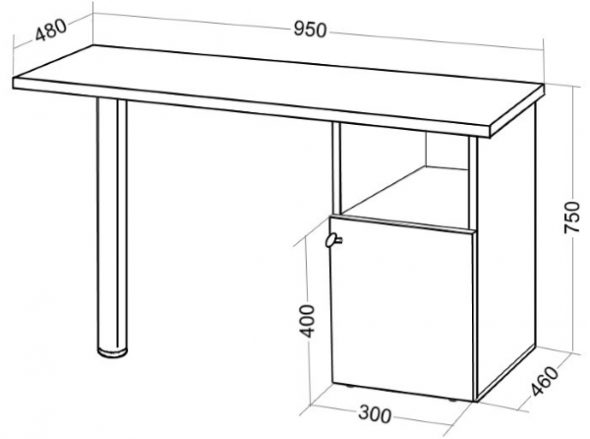
Manicure table with a cabinet - drawing with basic dimensions
The best option is still the cabinet, there you can remove larger items. The surface of the table top can be decorated with mini showcases. These are crossbeams of small width, allowing to place on them frequently used working tools. It is important that the table does not have long bases that support it. To save space in a small room, you can use a table that will unfold. For the manufacture of such things can be used as a basis for the design of the table-book.
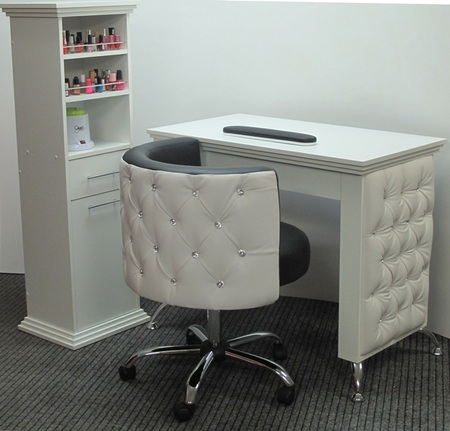
Unusual set for the manicurist - a table and a chair with a carriage coupler and a low narrow cabinet for materials and tools
How to make a manicure table at home?
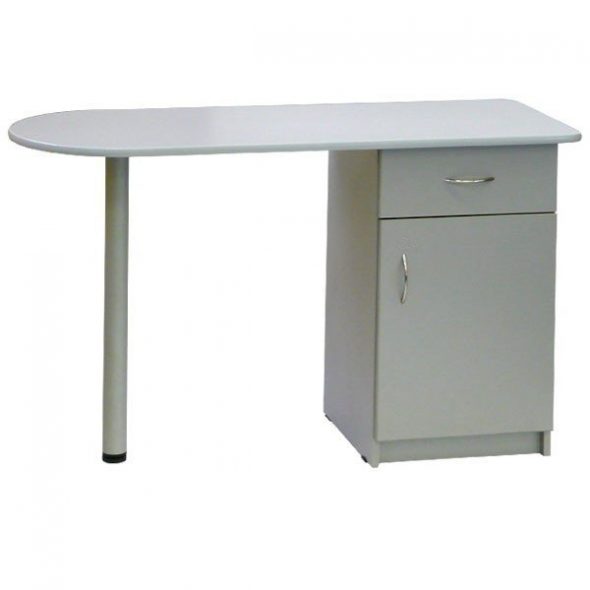
White table with cabinet for professional manicure
In this article, it will be considered the manufacture of exactly professional equipment that has a bedside table and emphasis on one leg.
In fact, the manicure table is made from any building material at hand. The best raw material for such works is sheet wood, it can be of the following types: MDF, chipboard and chipboard.
What you need for making
To make the table for the master of nail service will require:
- Laminated chipboard 16 mm;
- PVC edge 2 mm (for table top);
- PVC edge 0.4 mm (for other parts);
- leg for the table (thick metal);
- handle for cabinet lockers;
- screws, confirmatics, eccentrics and rods for them;
- dowels 10 mm - 16 pcs .;
- four-hinged furniture hinges - 2 pcs .;
- holders for shelves (can be replaced with dowels) - 4 pcs .;
- PVA glue (or wood glue).
Tools required for manufacturing:
- scissors;
- metal ruler;
- drill;
- screwdriver or Phillips screwdriver;
- hexagons;
- iron;
- pencil, meter and tape measure;
- electric jigsaw
detailed instructions
- First stage. We cut out parts for product assembly according to the following parameters: door (40 * 30 cm), bottom panel (46 * 30 cm), back wall of the bedside table (75 * 30 cm), side walls (75 * 46 cm), large shelf (45 * 29 cm ), a small shelf (45 * 28cm), working surface (tabletop) (95 * 48cm).
Cut pieces made of laminated chipboard for manicure table
- Step two. We glue the side parts of all parts with the edge of polyvinyl chloride. For convenience, it is better to fix every detail on special clamps. We apply to the surface edge, cut off with a margin and put the heated iron. After the glue has melted, remove the iron and smooth the surface with a soft cloth. Since the glue instantly freezes, it needs to be done very quickly. Excess edges cut with a metal ruler. It is very important to remember that a thin edge is glued with the help of an iron very easily; when using a more dense edge, edges are first processed with a mill. For the glue to melt, a hair dryer used in construction work is taken.
The ends of all parts must be pasted over with PVC edge
- The third stage. We collect a bedside table. In order for the fasteners to tightly connect the parts, it is necessary to make two holes in the side machines for the 45 * 29 cm shelf and two holes on the other side. Shelf will be mounted on the dowels, just with their use we collect the nightstand completely. To dowel well entrenched, we moisten them with glue.
We make holes and insert dowels in them
- Stage Four. Screw the eccentric rods inside at a distance of 1.5 cm from the hole made under the shelf 45 * 29 cm.
- Fifth stage. In the canvas prepared for the back wall, we drill four holes, put glue on the fixing parts of the PVA and place them in the holes. In the details of the shelf 45 * 29 cm we drill holes, retreating from the edge about 1 cm, on the side parts of the part we make holes for eccentrics.
We work with the back wall of the cabinet and with the shelf - we drill holes according to the scheme
- Stage Six. We fix the fasteners on the side with glue, install the shelf and fasten it.
- Seventh stage. We take the second part of the partition, smear it with glue and connect it to the shelf with a size of 45 * 29 cm, using previously prepared eccentrics.
Fasten the side to the big shelf
- The eighth stage. It is necessary to make holes, departing 20 mm from the edge of the part. For this, we use the Forster drill. Using screws, we fix the door hinges with four hinges. In the same way we fasten the counter strips, departing from the edge of about 3-5 cm.
Making holes for the hinges and fasten them with screws
- The ninth stage. We finish the assembly of the bedside table. It is necessary to turn it over and drill a hole with a diameter of 5 mm. In the bottom should be the same hole for better connection. The strength of attachment will provide the dowels greased with glue. Also for these purposes eccentrics can be used. To use them you need a Forster drill. With regards to the legs of the table, they can be bought ready-made or made from small bars and secured to the bottom using self-tapping screws.
We turn the cabinet and drill the holes for the dowels, then we lubricate the dowels with glue and insert it into the sidewall, top it with the bottom
- Stage ten. Now you need to attach to the surface of the table leg. To do this, using a screwdriver, make two holes approximately 20-25 cm from the edge. In these holes we put shkant and eccentric. This mount is suitable for portable equipment.In the manufacture of this object to be constantly in one place, you can use the corners, which are fixed to the surface with dowels, as fasteners. Make sure that the holes are made to coincide with the side panels. To be sure it is best to chart them with a pencil.
To the surface of the tabletop fasten leg
- Final eleventh stage. We fix on the curbstone tabletop. For a small shelf, it is necessary to insert holders for the shelves into the holes made in advance and place it on them.
Fasten the tabletop to the cabinet, insert the shelf holders into the holes and install a small shelf on them
Manicure table with hood
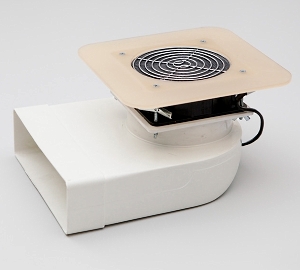
Extractor for manicure table
If you want to equip your table fully professional and make a hood in it, you can buy it in a store or make it yourself.

An example of a manicure table with a cabinet and installed hood
It is rather simple to make the exhaust vacuum cleaner. This will require a small electric motor with a capacity of up to 60 watts with blades. You can find it in any device. If you have an old kitchen fan or cooler from a computer, then they will be an excellent basis for the manufacture of hoods. It is important to find a power supply that will have the appropriate voltage for this device. When used as a basis for a kitchen fan, there is no need to look for a power supply, since it is already equipped with it.
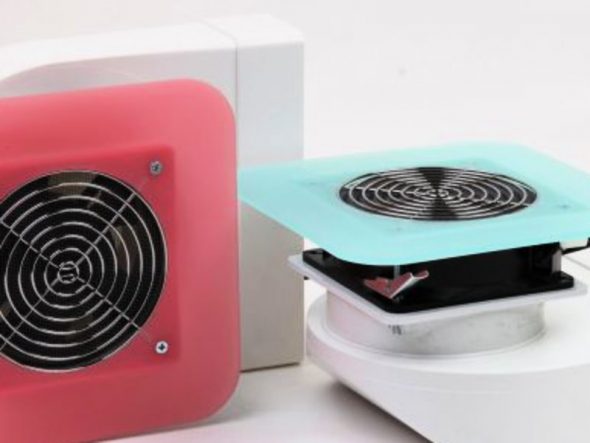
Extractor for manicure from the cooler
In the manufacture of exhaust vacuum cleaner from the cooler for the computer, you need a power supply that has the correct polarity. For such equipment, suitable blocks with a voltage of 5 to 12 watts.
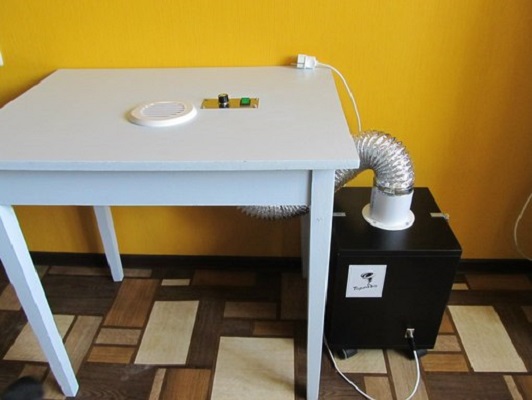
Vacuum cleaner for reliable air intake and ensure dust removal
Having decided on the basis for the working part, consider ways to remove dust and air entrapment. They must be reliable. If you are planning to make a portable hood, then a material such as plastic is very suitable for its body. It is easy to handle and does not have much weight during transportation.
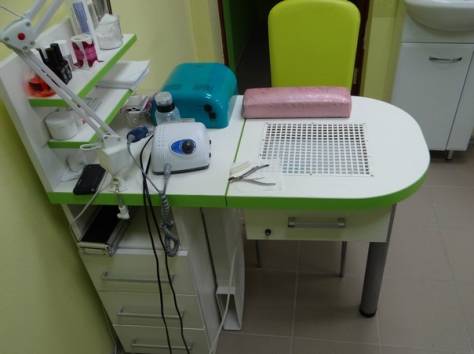
Convenient and functional manicure table with built-in vacuum cleaner
It is important to properly cut a hole in which the fan casing will fit and just as well to fix it well. Plastic is also very good as a base for fixing the protective grid.
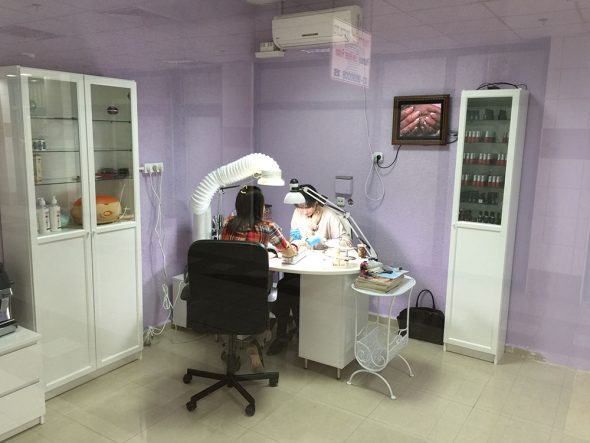
Powerful floor-mounted appliance for large salons where regular intensive ventilation is required.
For dust pins in a special bag of dust collector, on the back of the flexible plastic hose is attached, it is important to choose it exactly the diameter. The material at hand can be an excellent basis for a dust collector.
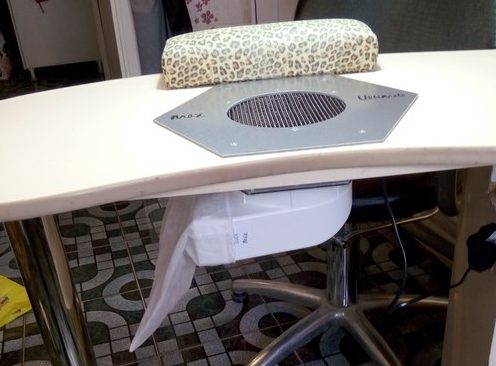
Vacuum cleaner for manicure table with replaceable dust bag
In the manufacture of stationary exhaust, which will be in one place, you should use flexible hoses for exhaust. They are made of materials such as plastic and acrylic, having a corrugated appearance. Such hoses are easy to find at any hardware store. It is better to display this type of hood in a window or a general exhaust system. This will save you from frequent cleaning of the dust bag.
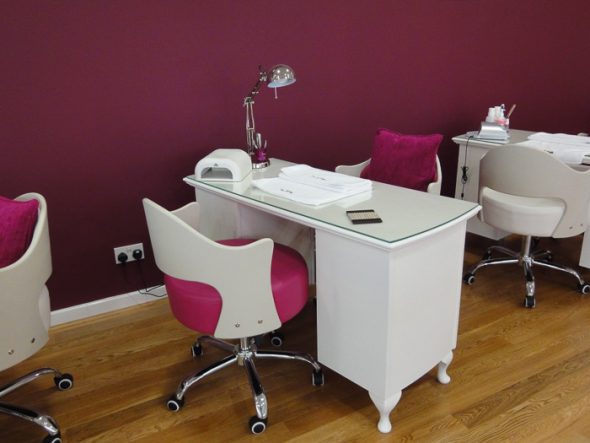
Necessary attribute of the nail master is a good manicure table
Video: Folding manicure table
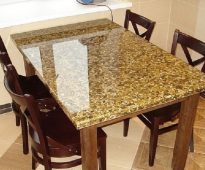
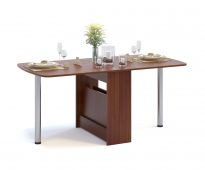
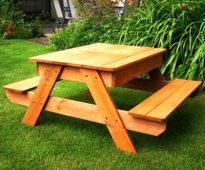
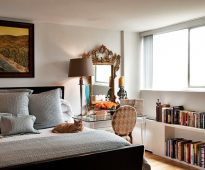
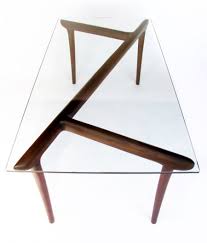
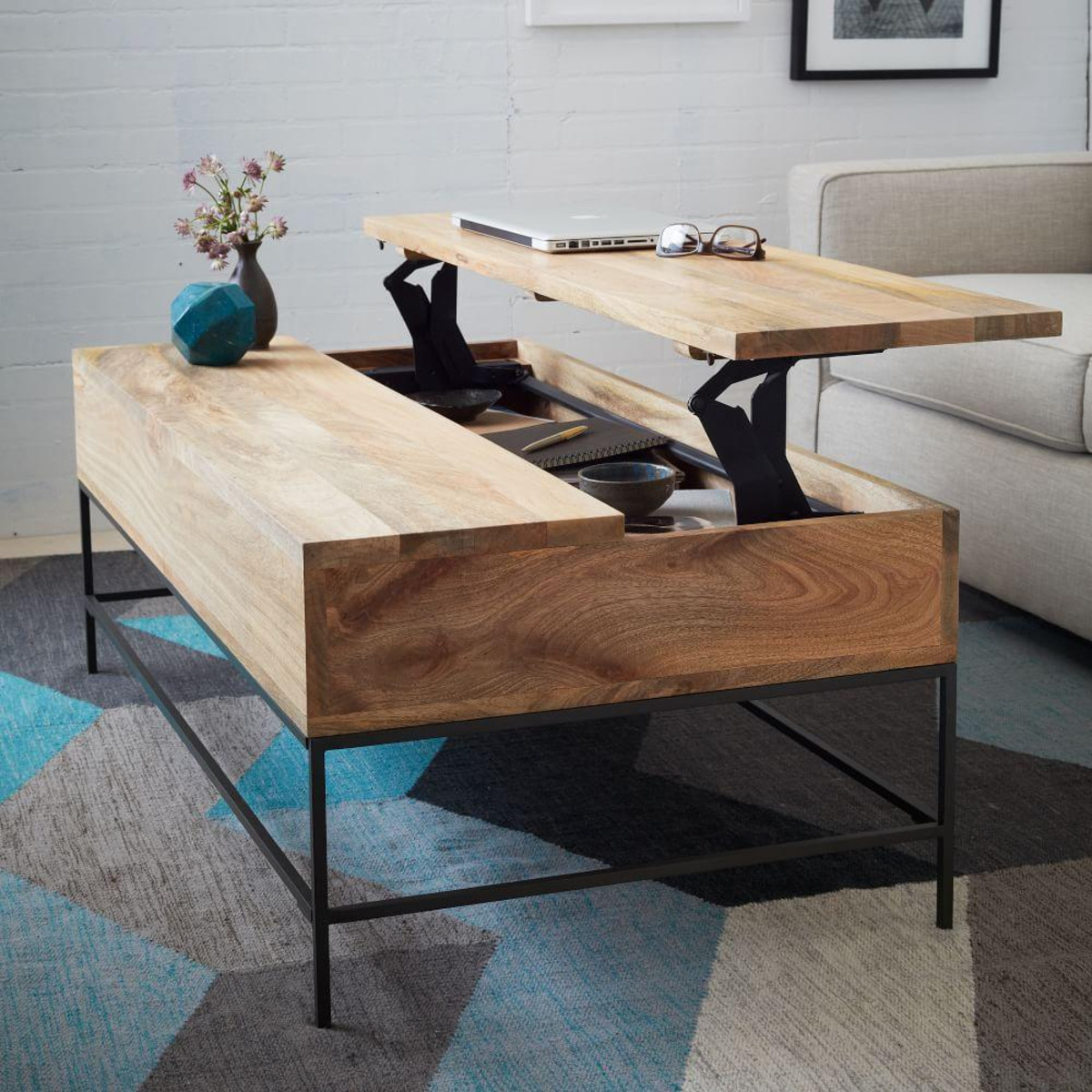