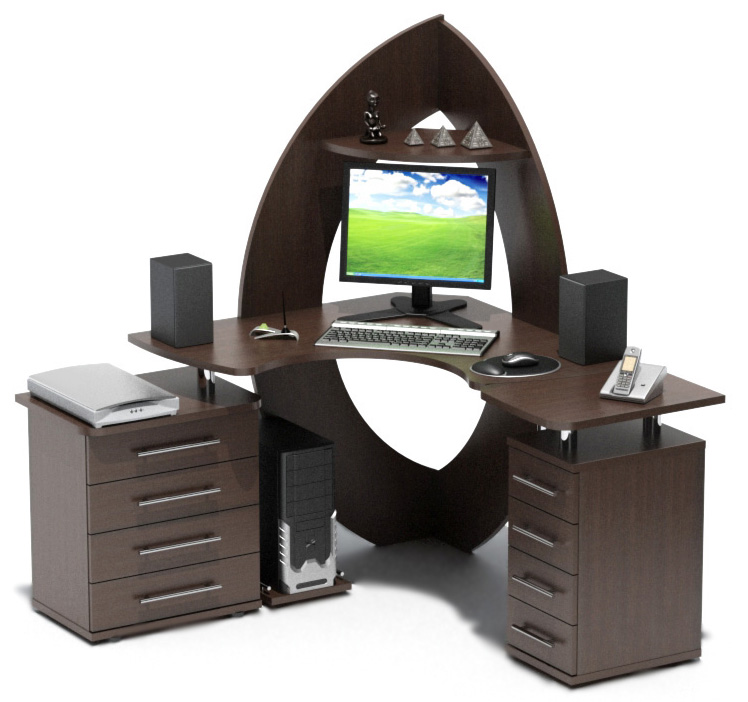
How to make a table of epoxy resin: design features and workmanship
The epoxy table looks unusual. Through the use of this material it is possible to make unique designs that look favorably in any interior. With the use of resin, you can turn an ordinary wooden product into a real piece of art.
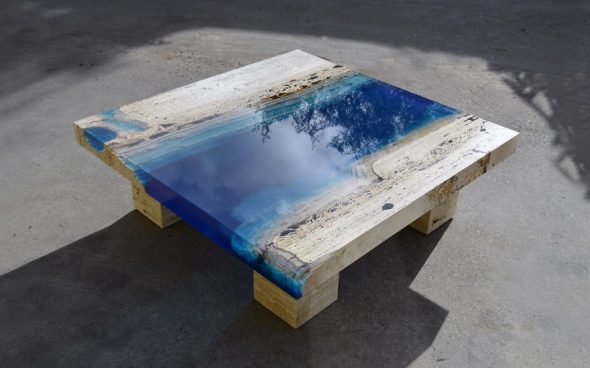
The epoxy table looks unusual.
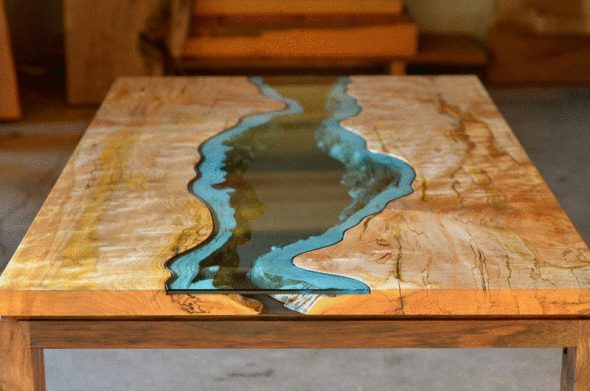
Through the use of this material it is possible to make unique designs that look favorably in any interior.
Content
Material Features
Epoxy resins are a synthetic compound of oligomers. In the "pure" form, this material does not apply. Its properties appear only after contact with the hardener.
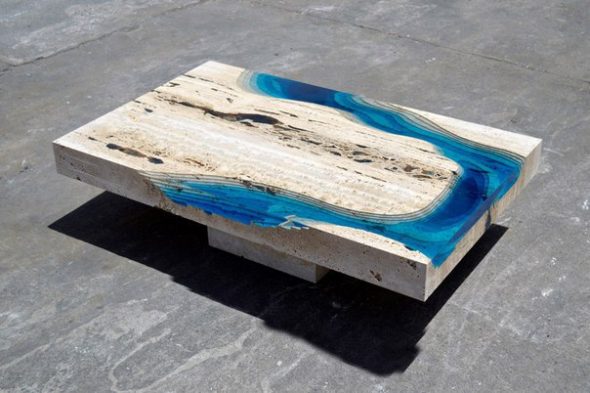
With the use of resin, you can turn an ordinary wooden product into a real piece of art.
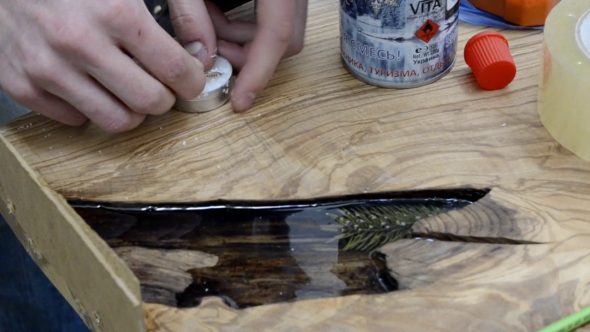
This material is not applied in “pure” form.
Changing the combination of the main components can make resins with different characteristics.
- solid;
- liquid;
- high strength;
- rubber-like and others.
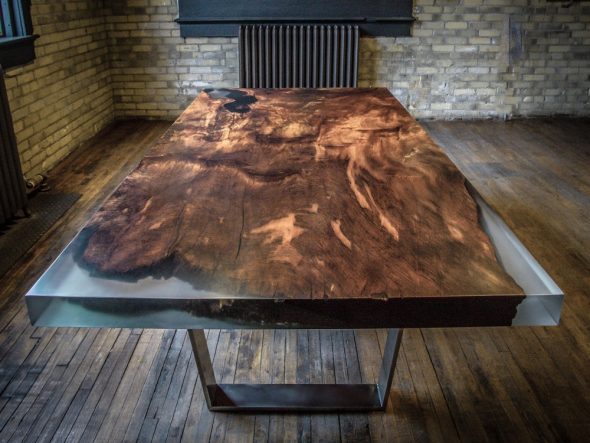
Epoxy resins are a synthetic compound of oligomers.
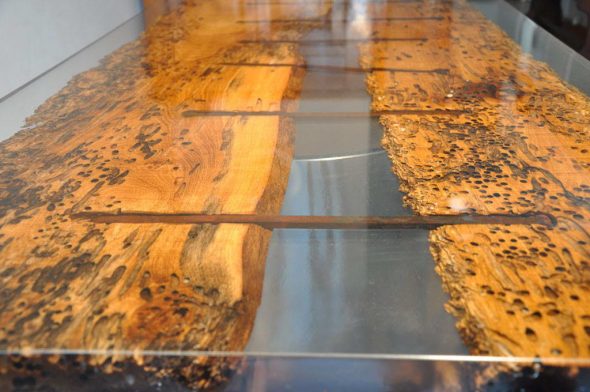
. After that, the product can be used as intended.
The scope of epoxy resin depends on its modification. The list and features of the latter are given in the table.
Type of modification | Specifications |
Chemical | To get it, various chemicals are added to the resins that come into contact with them (polyester alcohols and others). These components change the characteristics of the main ingredient. |
Physical | The modification is obtained by adding a substance to the resin that does not come into contact with them. |
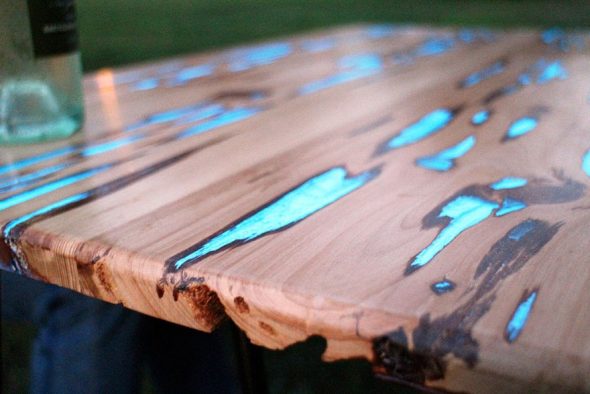
In the "pure" form, this material does not apply.
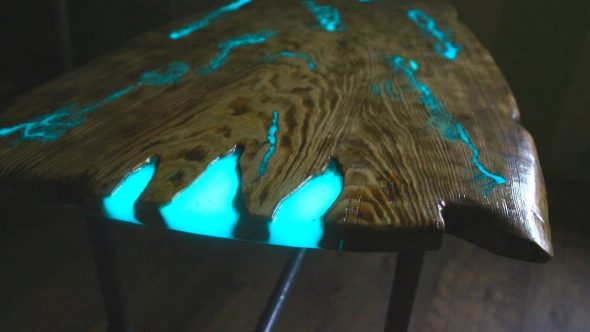
Changing the combination of the main components can make resins with different characteristics.
The table made of epoxy resin is made by applying a synthetic material on a wooden base. The result is a product that is characterized by increased resistance to chemicals.
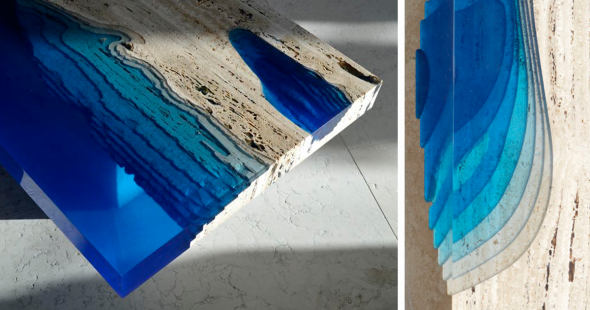
In the process of creating a structure, it is important to prepare a wooden surface, removing dirt from it.
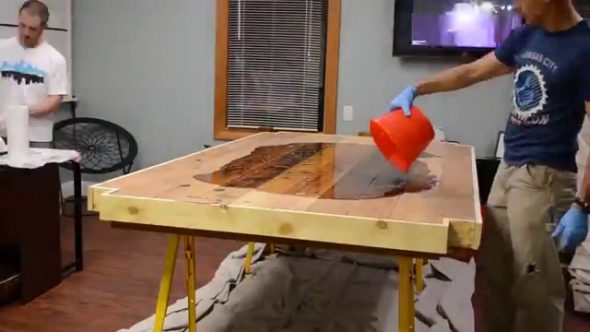
In the future, the surface of the table top will cover the air bubbles.
To make a table made of epoxy, it is necessary in addition to preparing a wooden base to mix synthetic material and a hardener. From the ratio of both components depend on the characteristics of the composition. Excessive or insufficient content of the hardener reduces:
- strength of the product;
- resistance to chemicals and water.
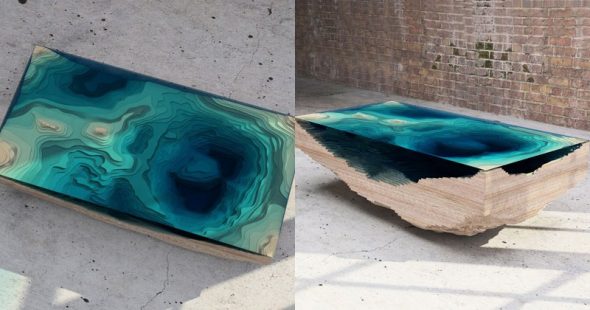
When choosing a table of epoxy resin should pay attention to the presence of bubbles.
In this case, the excess hardener out of the resin. In most cases, in the process of manufacturing various products using this material, the ratio of initial components is 1: 1 or 1: 2.
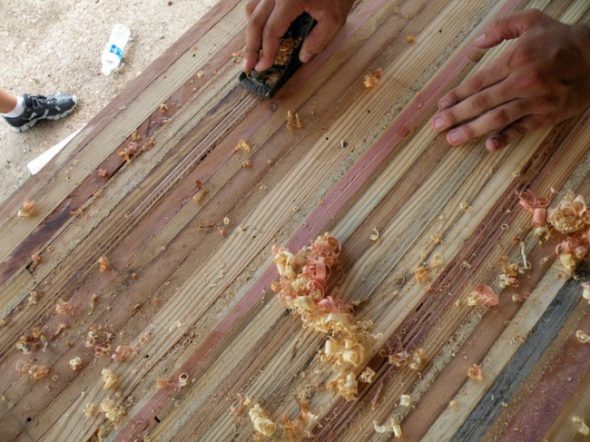
Among the disadvantages of tables made of epoxy resin should highlight their higher cost.
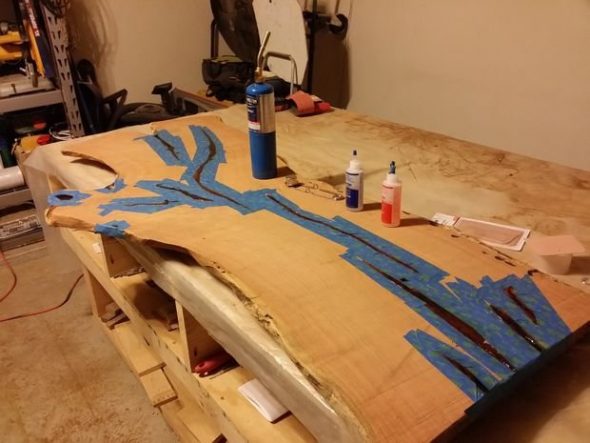
At the end of the preparatory stage, the epoxy compound (resin and hardener) is mixed in which, if desired, paints and other components are added.
Types of products
Tables of epoxy resin differ in appearance and features of synthetic material. The latter is cold or hot cure. For the manufacture of tables of epoxy resin in the home mainly used the first type of substance.
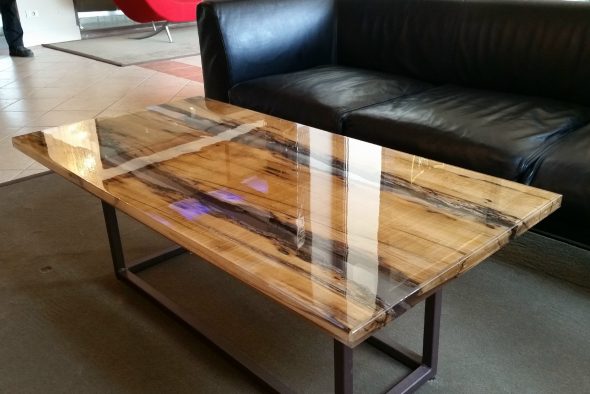
In the process of hardening, the synthetic composition practically does not shrink.
Advantages and disadvantages
Tables made of epoxy resin have the following advantages in comparison with standard wooden structures:
- have a unique appearance;
- waterproof;
- not subject to abrasion;
- unlimited possibilities for design decisions.
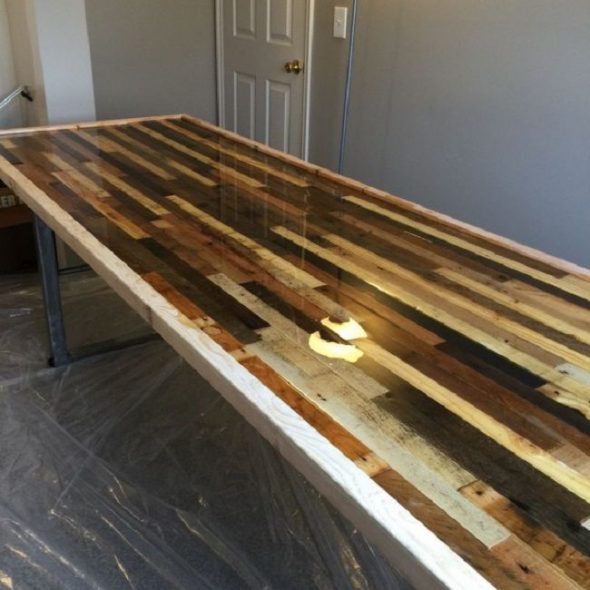
Tables made of epoxy resin have the following advantages in comparison with standard designs made of wood.
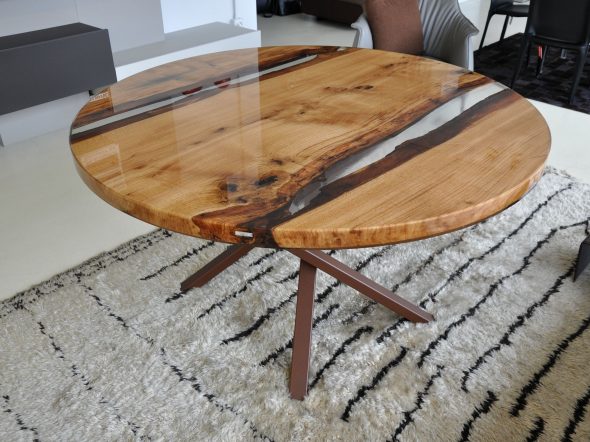
The resulting substance is applied to a wooden surface.
In the process of hardening, the synthetic composition practically does not shrink. Tables of epoxy can be made using additional materials:
- phosphorescent and other paint;
- rubber;
- corks from wine bottles and so on.
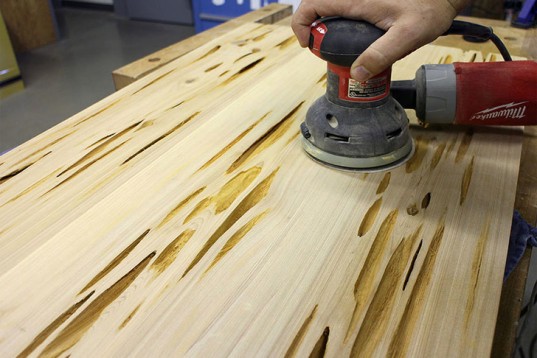
For the manufacture of tables of epoxy resin in the home mainly used the first type of substance.
Among the disadvantages of tables made of epoxy resin should highlight their higher cost. Depending on the type of construction, size and design, the price for covering one product takes several dozen liters of synthetic material.
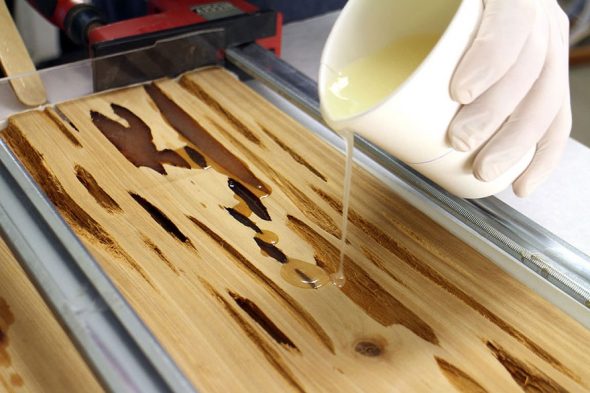
Tables of epoxy resin differ in appearance and features of synthetic material.
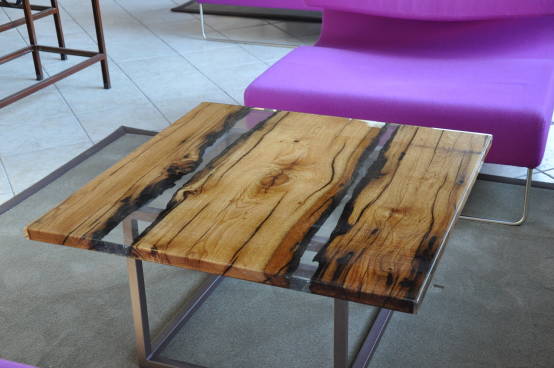
To remove the air bubbles that appear, you should warm the surface with a building dryer.
When choosing a table of epoxy resin should pay attention to the presence of bubbles. They appear due to non-compliance with the manufacturing technology of the product and adversely affect its characteristics.
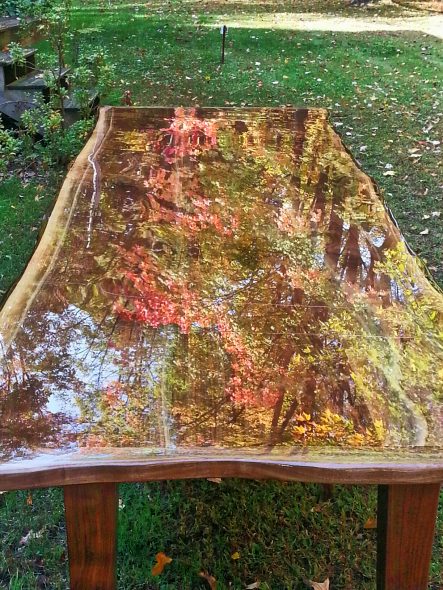
In most cases, in the process of manufacturing various products using this material, the ratio of initial components is 1: 1 or 1: 2.
In the process of creating a structure, it is important to prepare a wooden surface, removing dirt from it. After that, the material should be primed, as the resin is well absorbed into its pores. In the future, the surface of the table top will cover the air bubbles.
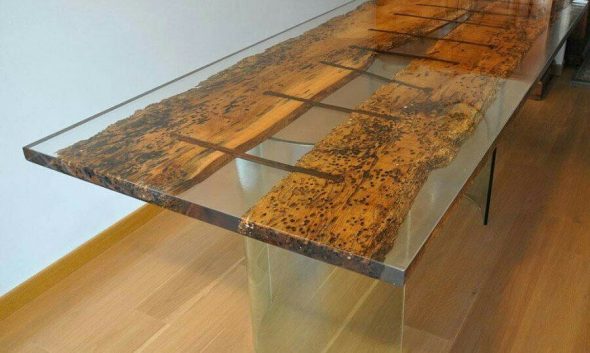
To make a table made of epoxy, it is necessary in addition to preparing a wooden base to mix synthetic material and a hardener.
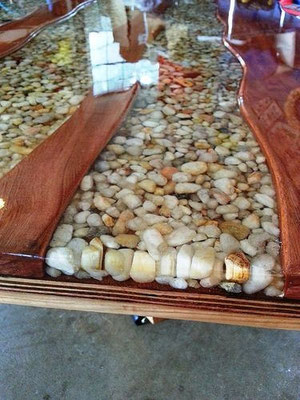
At the end of the tabletop is ground and polished.
At the end of the preparatory stage, the epoxy compound (resin and hardener) is mixed in which, if desired, paints and other components are added. The resulting substance is applied to a wooden surface. On complete hardening takes about 15 minutes. To remove the air bubbles that appear, you should warm the surface with a building dryer.
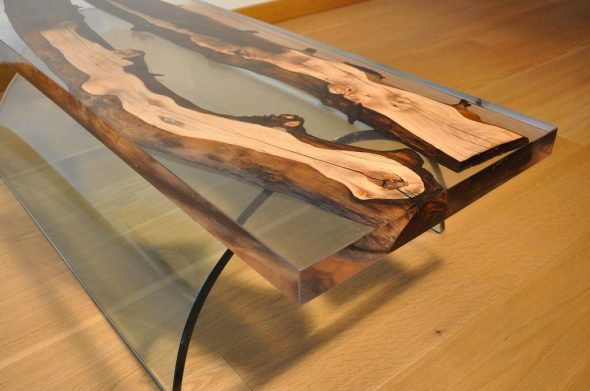
The table made of epoxy resin is made by applying a synthetic material on a wooden base.
At the end of the tabletop is ground and polished. It takes about 7 days to manufacture the whole structure, during which the material gains strength. After that, the product can be used as intended.
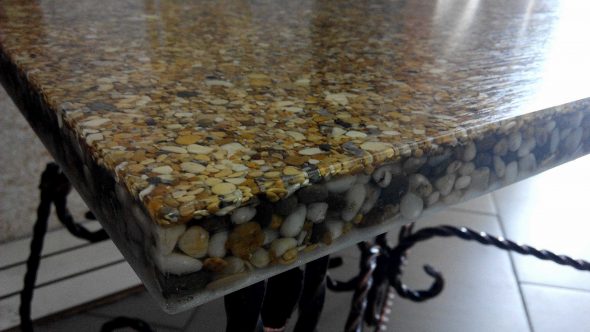
The scope of epoxy resin depends on its modification.
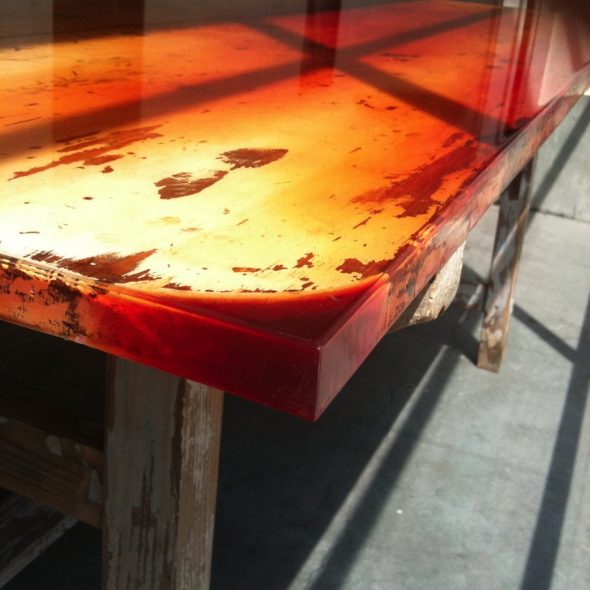
It takes about 7 days to manufacture the whole structure, during which the material gains strength.
VIDEO: withepoxy and slab tol
50 photo ideas of epoxy resin table design
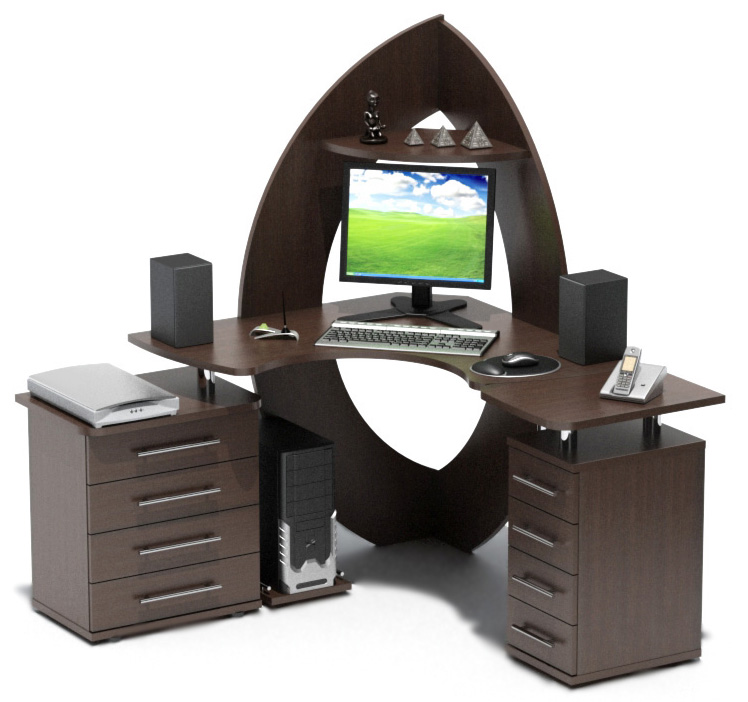
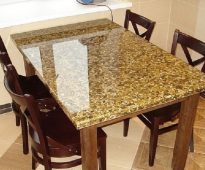
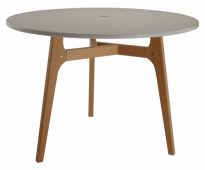

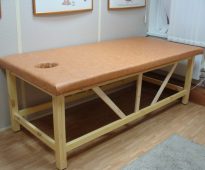
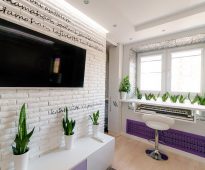
The article would need to be corrected. The message seems to be clear, but an understanding of the essence of the resin, advantages, such as universal properties, are completely absent. What about chemistry, not the correct wording: From what end did polyester alcohols come from? Curing takes place mainly in the Amine type. It is in these that the curing process takes place at T at 10-35 ° C. Such a process of (cold) curing is often practiced in small-scale production in terms of souvenir, gift products, advertising business, interior decoration, and the manufacture of large plastic parts for passenger transport. So ‘friendly’ polymer that would be so different, durable, lightweight and non-toxic to humans.
What about the minuses, such as instability to UV radiation? That is, there is no place to take it out, do not use UV llamas to disinfect the premises .. Or am I mistaken?
what wood can i use
And how does the tree stay exactly in the middle of the resin?
Just fantastic! Can a kitchen worktop be made of resin?
What kind of resin is used for such products? Can you advise?
I wanted to do the manufacture of such tables, table tops, and so on. What advise, which pitches are better, which firms are more profitable. Thanks in advance for the answer
Please tell us all the nuances of this production:
Cost price
Technology
Necessary equipment
Thank!