
We make shelves in the garage with our own hands: practical advice, recommendations
The main purpose of the garage is to store cars. However, this does not prevent car owners from using it for other purposes: storage of conservation, tools, household appliances, unnecessary things, car parts. Over time, the mountains accumulate various household accessories. The garage is slowly turning into a chaotic dump, the place is getting smaller. This is a sign - it's time to competently organize the space, by installing shelves in the garage. They will allow you to rationally place things, save usable space, improve the interior of the room.
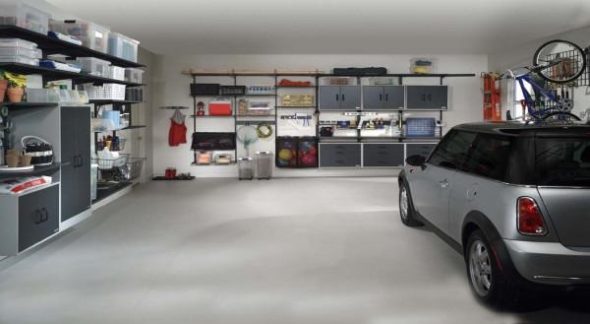
Garage with convenient storage when everything is in place
Racks in the garage with their own hands to make quite simple. You need to prepare the tools, buy some materials, release a few hours from work. In this article we will look at detailed instructions, some tips, recommendations on the arrangement of such a structure.
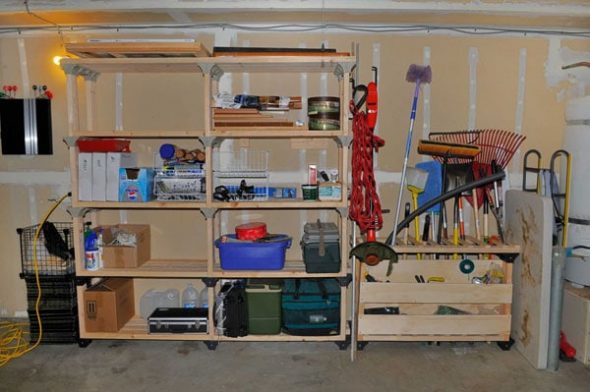
Shelving with storage shelves
Content
- 1 Welded, bolted rack: which is better?
- 2 We are determined with the design
- 3 Choosing a material
- 4 The advantages of creating your own hands
- 5 Required Tools
- 6 Manufacturing process: step by step instructions
- 7 Video: Shelving in the garage with his own hands. Collapsible / Demountable Garage Storage Shelves. DIY.
- 8 50 interesting design options shelves in the garage:
Welded, bolted rack: which is better?
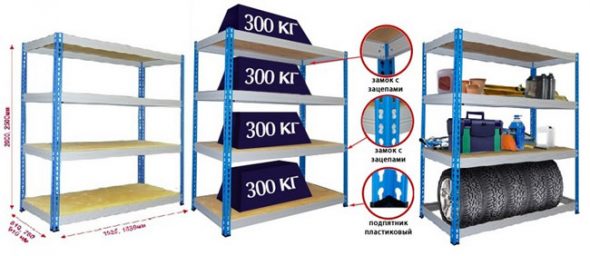
Allowable loads on homemade shelves in the garage
Before planning the shelves for the garage room, you need to determine a more convenient way to fix them. Today two methods are most popular: welded, bolted. Welded technology is commonly used for metal structures, bolted - wood. Both technologies are working properly. Such shelves in the garage are convenient during operation, can withstand heavy loads. However, they have some drawbacks.
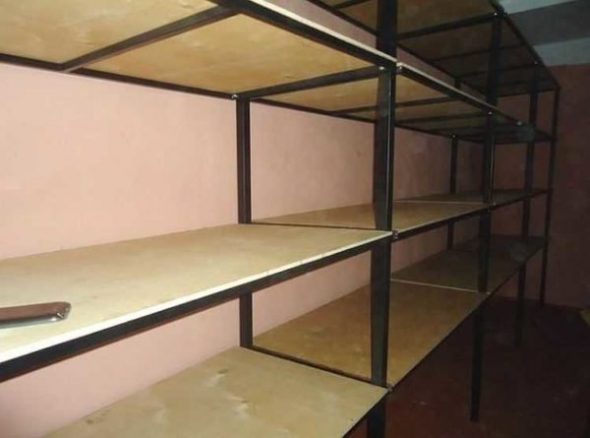
One of the options of racks with a frame made of a profile pipe and shelves of plywood
Welded shelves are non-separable. When changing the garage plan, its purpose, just disassemble the product will not work. Transporting welded shelves is also uncomfortable. Their weight can exceed one hundred kilograms. The main advantage of this design is its reliability. Welding seams firmly fix the elements among themselves. To achieve their destruction is not easy at all.
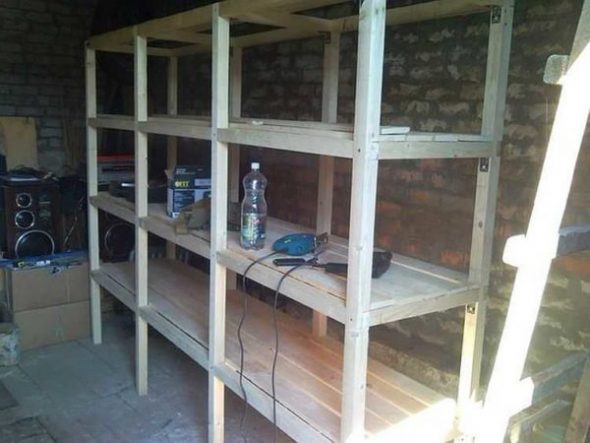
It is better to connect the wooden rack for the garage on nails rather than on screws, so they are less loose
Bolted racks are less stable. They can not provide sufficient rigidity. For stability, the structure has to be additionally fixed to the wall. However, there is a significant plus in this method of attachment - mobility. Shelves can be disassembled, assembled, make hinged shelves of various sizes. It is impossible to give an unequivocal answer to the question which technology is better. Each person will be important to their own parameters.
We are determined with the design
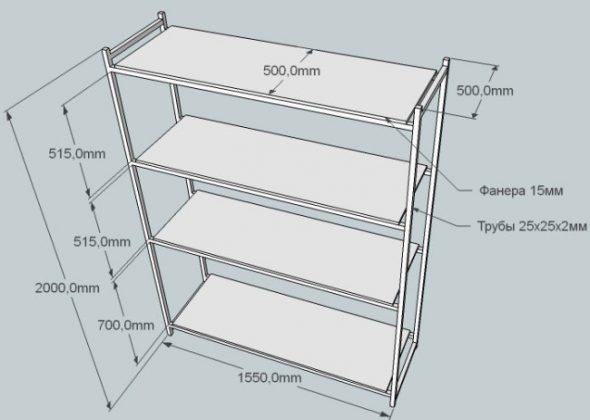
The scheme of the simplest rack in the garage
Making racks in the garage with your own hands is pretty simple. The most important thing is to clearly define your own desires, needs, plan the design, type of construction in advance. Such tasks can be done by anyone, especially if you have a great desire to do something yourself.
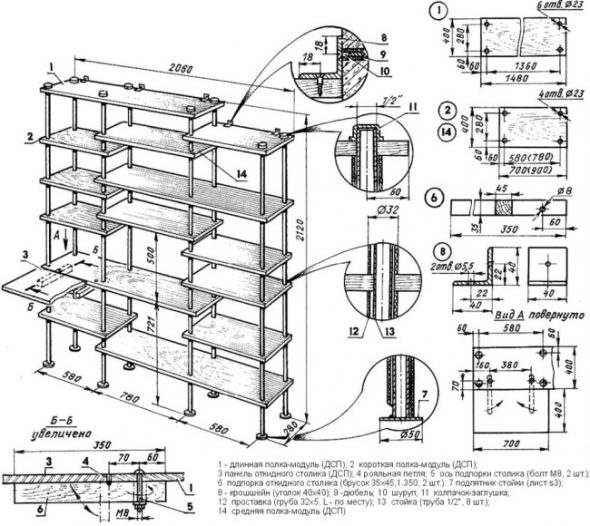
Drawing rack of pipes with wooden shelves
The design of the shelves has three elements: vertical racks, shelves, rails. In some cases transverse tightening is used. They are not required. Only needed to increase the rigidity of the frame. To determine the exact version of the design of the future rack, follow these recommendations.
- Depth, height of shelves - any. These parameters are selected only on the basis of the purpose of the niche. Each shelf can be designed to store a certain type of items. All this is best decided in advance;
- The distance between the vertical posts should be selected based on the stiffness of the material. For very heavy accessories, the distance should be about 1.5 meters. For a long rack it is necessary to prepare intermediate vertical racks. They will make the system more stable;
- Bottom shelves should be some distance from the floor. Approximately 50-70 cm. Heavy objects should be stored on them. The optimal height of the remaining shelves will be 37 cm. This is the most rational height, often used in the manufacture of any furniture structure.
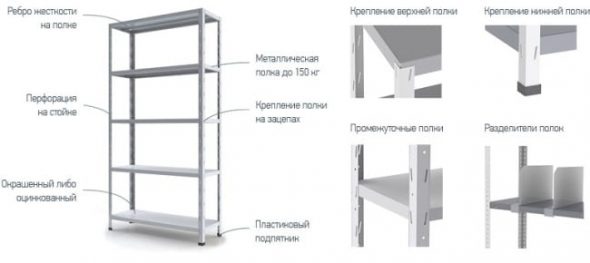
Drawing of a metal rack for the garage
It is always easy to determine the design features. The owners of the garage simply take into account the dimensions, features of things that will be stored in the design.
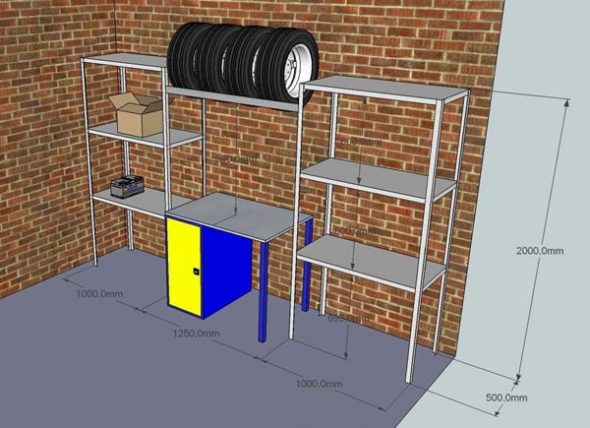
Option for a small garage with a workbench
A little harder to choose product design. The garage is designed for practical purposes. However, this does not mean that its interior should be boring, ugly. In the garage room you can easily make an attractive interior for little money. In particular, you can decorate the design of the rack with ordinary paint. Today there are paints designed for any materials. Color for painting should match the overall color of the room. A certain decoration will be colored plastic boxes for storing supplies and tools. They are inexpensive, allow you to bring perfect order.
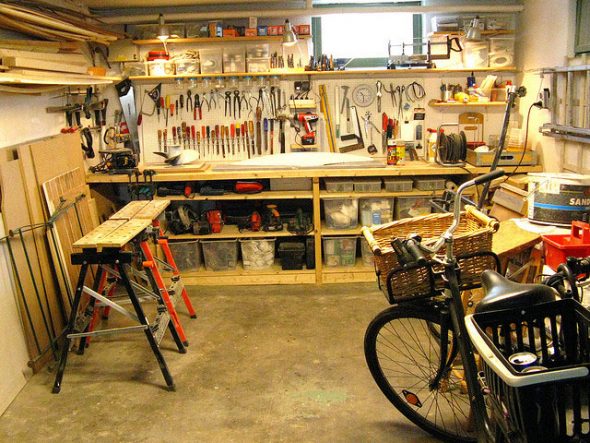
Transparent and colorful plastic boxes for shelves in the garage
Choosing a material
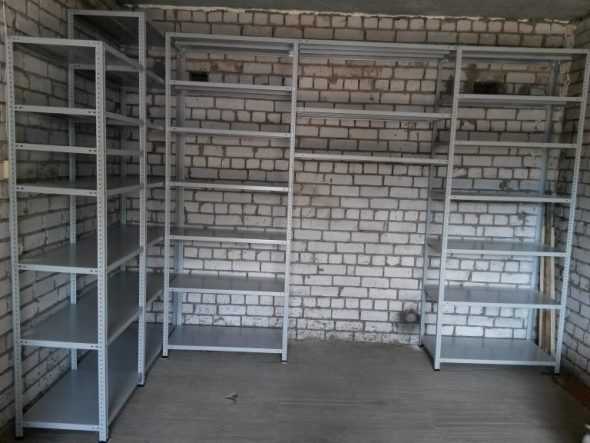
Durable metal shelves in the garage
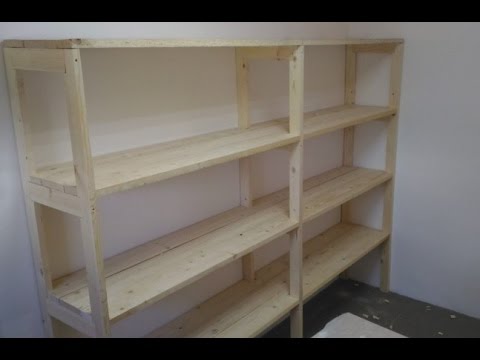
Handmade wooden shelves in the garage
For design, the stability of the frame, the practicality of operation of the construction plays a huge role the choice of the base material. The rack can be made from different raw materials, which has its advantages and disadvantages. Consider the main types of materials, their features in the table.
Material | Advantages disadvantages |
Metal | Many car owners prefer it to the metal for its durability. Such material is durable, can withstand heavy loads. Only high humidity can have a negative effect on it. In normal climates, metal structures will last almost forever. Also, the advantage of such raw materials is ease of care. Products will need to periodically simply wipe with a cloth to maintain cleanliness. The main disadvantage of the metal is its high price. However, many have unnecessary pieces of metal in the country, with friends. Metal elements dock, usually with a welding machine. It is not recommended to use it without proper experience. |
Tree | Wood is a noble, useful raw material. From it excellent hinged regiments, racks, systems of storage turn out. Wood has a very positive effect on the respiratory system of a person, has an attractive appearance, is easy to process. In the manufacture of storage systems, you can use oak, pine, birch. The frame should be fixed only with metal bolts. Wood is relatively inexpensive. It can be purchased at any building hypermarket. The disadvantage of this option is the difficulty in care. The tree gets dirty, it can darken, rot. You should constantly look after him. This is not always convenient. To reduce such negative effects it is recommended to apply special impregnation. |
Plastic | A good option for storing various small items, lightweight accessories. Plastic has been used for the manufacture of shelves relatively recently. It can withstand no more than 75 kg. It is worth considering! The advantage of plastic is low weight, mobility, ease of care, low price. The downside is fragility. It is easy to damage, beat. Plastic storage is not suitable for storing metal tools. |
Combination of two materials | For example, wood and metal. This is a great option for creating a multi-functional storage system. In this way, you can save money, diversify the design of the garage, simplify the process of manufacturing the structure. You can combine almost any type of raw materials. |
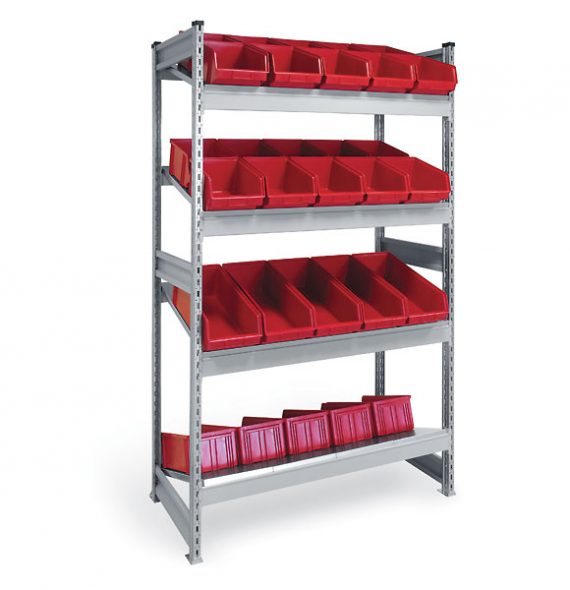
Rack metal collapsible with plastic containers
The advantages of creating your own hands
Many ask a logical question: is it better to make shelves in the garage on your own or to buy a ready-made version on the market? Consider the main advantages of self-creation of a garage storage system.
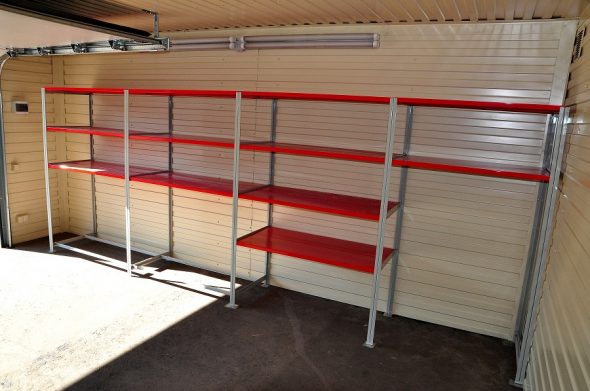
Collapsible racks have an aesthetic appearance and are convenient for assembly and disassembly.
The possibility of developing a unique design. For many car owners, a garage is a real pride. I don’t want to put ugly furniture in it. Standard shelves are also a little attractive. In this case, you can take on the job yourself by inventing a unique design. Ideas for implementation can be viewed on the Internet. But it is better to give free rein to their own fantasies.
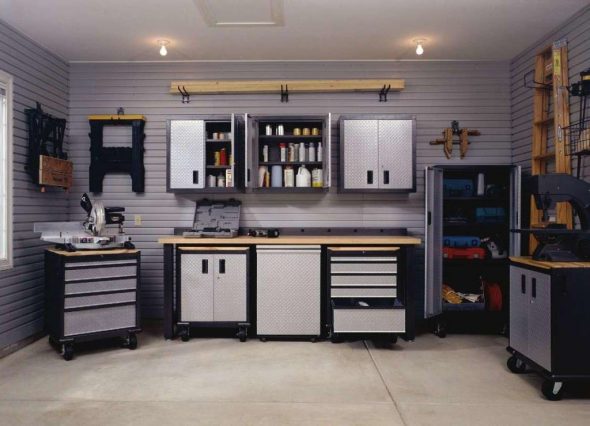
The idea of arranging the garage from the inside with your own hands
To make hinged shelves, shelving your strength is not as difficult as it seems. Such a task will be under the power of any man who has at least minimal experience working with tools.
The manufacturing process does not take much time. Lack of free time - the main reason why car owners buy furniture for the garage in the store. However, the manufacture of a storage system does not require huge time-consuming. Enough to allocate a few hours, call for help from a friend.
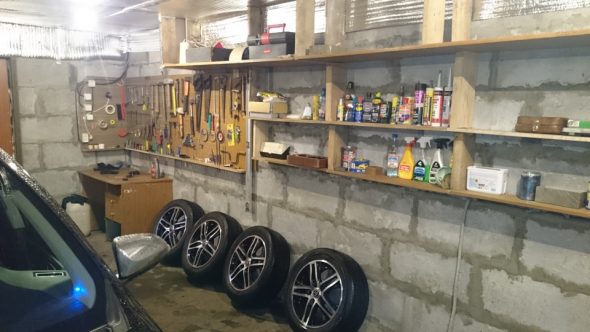
Homemade shelves and racks for the needs of the owner of the garage
Shelves can be made on a personal plan. Only the car owner himself knows what size, depth, height he needs shelves. Find the perfect option in the store is almost impossible. In hypermarkets, everything is standard. It is better to make a little effort, to spend time, but to create the most practical thing.
Small financial costs. Storage furniture is quite expensive. Even the simplest models will cost a large sum. Self-manufacturing is the best solution in order to save money. Many of the necessary parts can be found in his household.
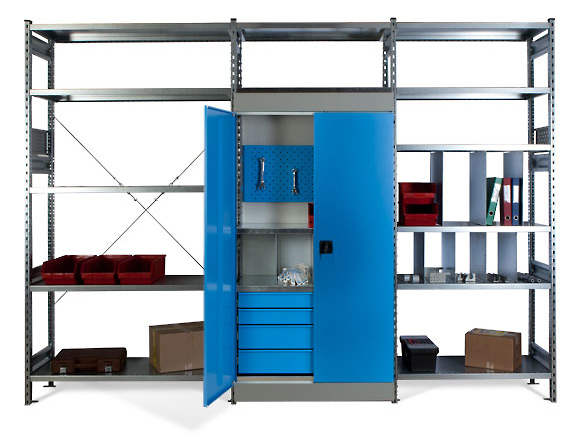
Cabinet built in racking system in the garage
Required Tools
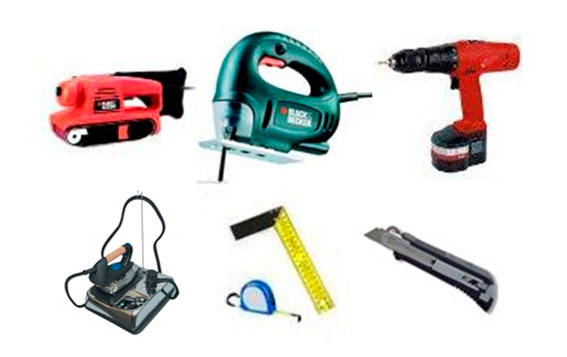
Necessary tools for the manufacture of shelves
To the process of manufacturing shelves took a minimum of time, you must prepare the tools in advance. It will take not so much: a set of wrenches, pliers, a hacksaw for wood, metal, a hammer, a screwdriver, a perforator, a jigsaw, a Bulgarian. All of these names have almost any good owner. A set of basic materials will depend solely on the choice of each individual. It can be plywood, metal pipes, bars, chipboard, plastic, and much more.
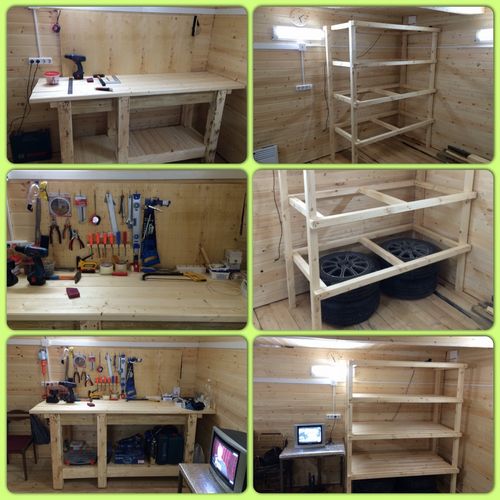
Popular options for storage of tools in the garage
Manufacturing process: step by step instructions
- Preparation of the place of work. Shelving - dusty work. Need a lot of space. For this car from the garage is better to remove. The film should cover the tools, expensive things. Next you need to prepare the tools, put them next. It is advisable to enlist the help of a friend. Together the work will be done as quickly as possible.
- Preparation of the plan. For ease of operation, a rack plan is best drawn in advance on a simple piece of paper. There you should also note the measurements of each shelf.In preparing the plan, you need to take into account specific things that will be stored on the shelves. It is not necessary to make a standard design. In one system, you can combine several different elements.
Holders and Net Shelves
Mounting mesh shelves on the side wall of the garage - a quick option for light objects
- Purchase of basic raw materials. It can be wood, metal, plastic. When choosing it is necessary to take into account the characteristics of the material, its maximum load, practicality. When buying is not worth saving, choosing raw materials of poor quality. It will not last long, will bring a lot of problems during operation.
- Cutting frame elements. The main elements can be made of wooden bar, steel angle, ordinary pipe. Racks, amplifiers, crossbars are cut using jigsaw, circular saws.
We start the manufacture of the rack with the base
- Marking on racks. Vertical elements must be marked. This will help in further installation of the crossbeams.
We make grooves for shelves a frezer
- Drilling holes. Neat holes are made on the markup using a drill. This is typical when using bolt hardware. When choosing a welded frame, all elements are joined by seams. In the absence of proper experience, the seams can be ugly. Also when working with welding, it is important to observe safety precautions. Read more about this in the instructions for the welding machine.
In the grooves set the shelf and additionally fasten screws
- Manufacturing shelves themselves. For them, usually choose plywood, boards, chipboard. It is important to accurately observe the measurements.
- Collecting the frame, fixing the shelves on the frame. The frame is assembled gradually: first, the side racks, then the crossbar, then amplifiers. Only then shelves. They are fastened with bolts, screws. The mount should be strong.
Install the rack on the base
- Giving an attractive appearance. Ready shelving can be painted, decorated by the author forging, glue film. The choice of designer accessories is highly individual. At the same time, one should not forget about practicality.
Video: Shelving in the garage with his own hands. Collapsible / Demountable Garage Storage Shelves. DIY.
50 interesting design options shelves in the garage:

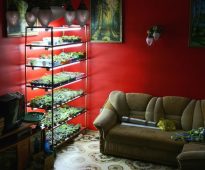
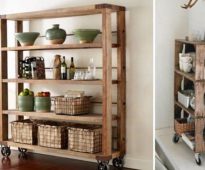
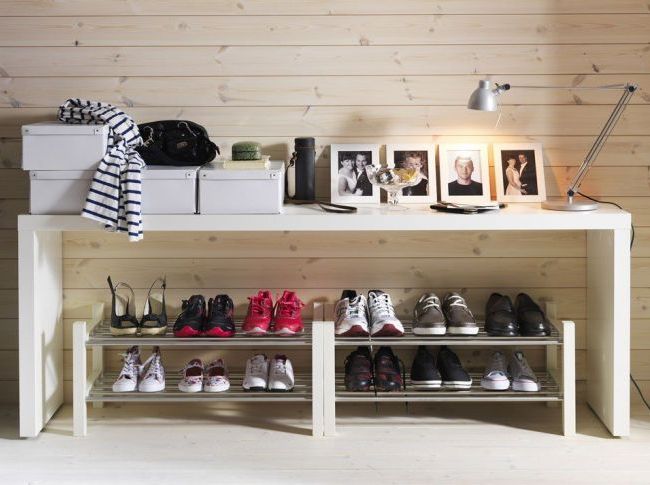
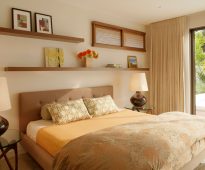
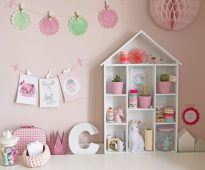