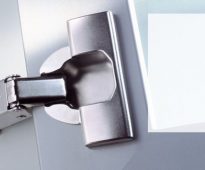
If the back wall - does not mean unimportant!
Cabinets can be made as a separate enclosure and built-in.
Built-in mounted directly to the wall of the room at the place of their location. The advantage of individual models is the ability to disassemble, move and put them in any place. Hull models always have the back wall of the cabinet. It isolates the interior of the cabinet, making it aesthetic, especially if the wall behind it is uneven, without finishing. The back wall of the cabinet rigidly fastens the entire structure, keeps it strictly upright.
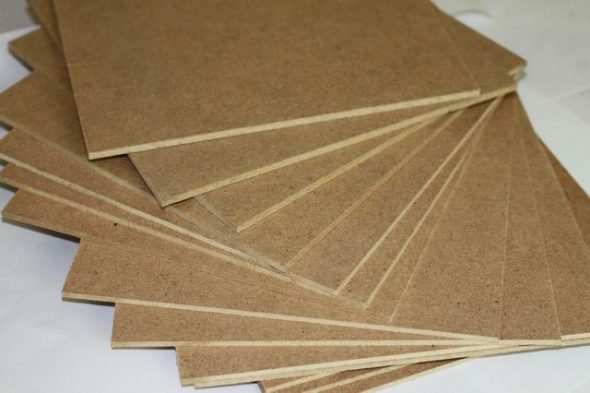
The back wall of the cabinet is made of wood fiber boards (DVP).
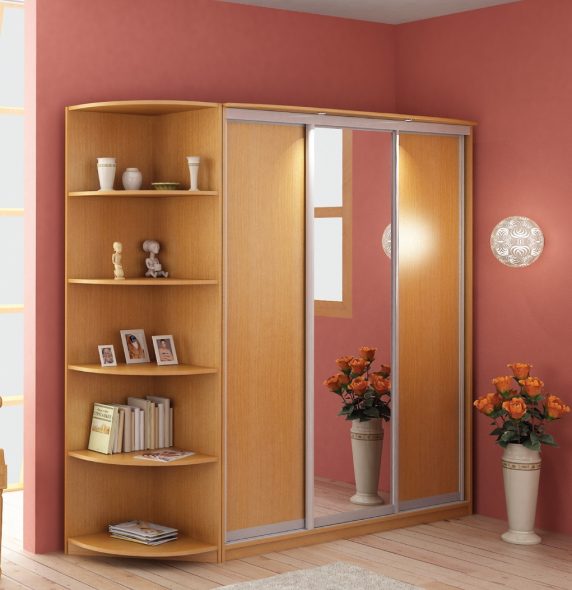
For safety and reliability you need
make of chipboard.
The sliding wardrobe is divided into sections, drawers, shelves and filled with things very unevenly. Under the influence of the load wardrobe compartment can be deformed. To prevent this, in addition to the rear wall, special stiffening ribs can be provided inside.
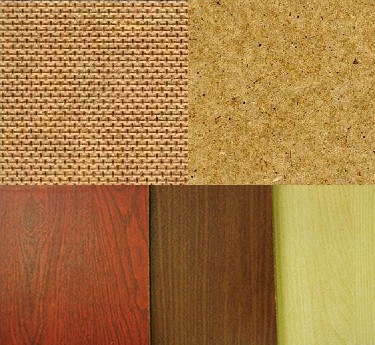
In addition to the rear wall, special stiffening ribs may be provided inside.
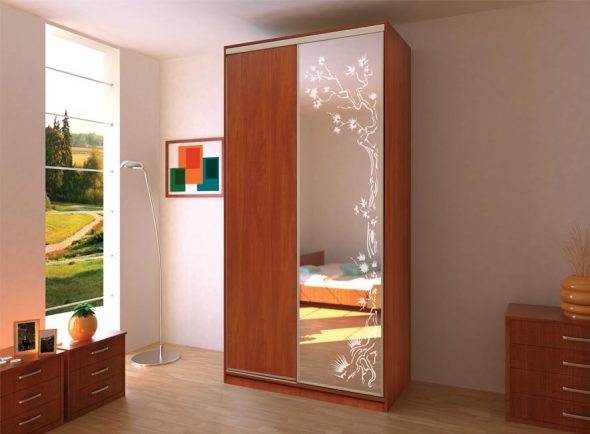
Fiberboards have a good
margin of safety.
Content
What is the back wall of the cabinet made of?
The back wall of the cabinet is made of wood fiber boards (DVP), laminated chipboard (LDSP).
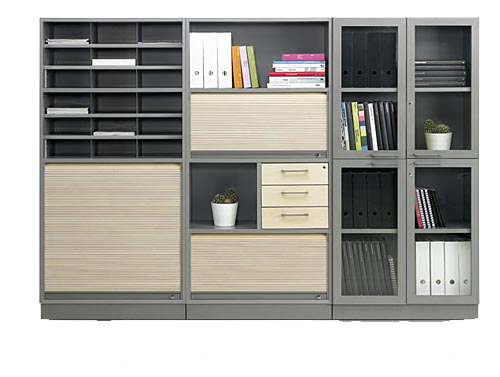
One sheet may not be enough to cover the entire back surface.
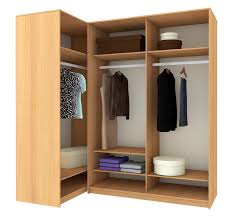
Some people suggest nailing the back walls of the cabinets.
Fiberboard consists of wood fibers, synthetic resins, fillers, water.
Differs:
- for general and special purposes;
- hardness - superhard, hard, semi-hard, soft;
- by thickness.
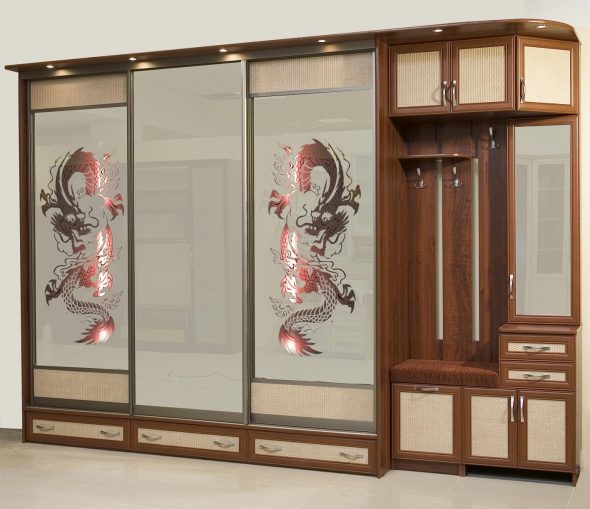
Under the influence of the load wardrobe compartment can be deformed.
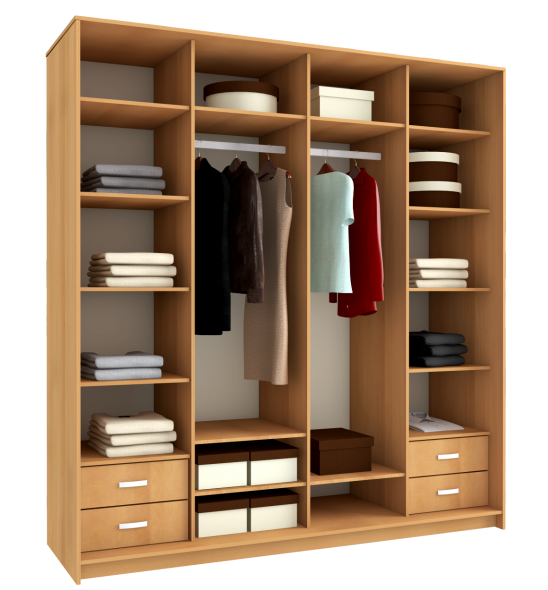
Not recommended and the use of construction stapler.
Plates can be smooth on one or two sides, varnished, covered with laminate film, artificial veneer. They also differ in the degree of response to moisture, fire resistance, exposure to sunlight. The most commonly used are solid species: small dispersion fraction (MDF) or hardboard and harder, modern material HDF from coniferous woods.
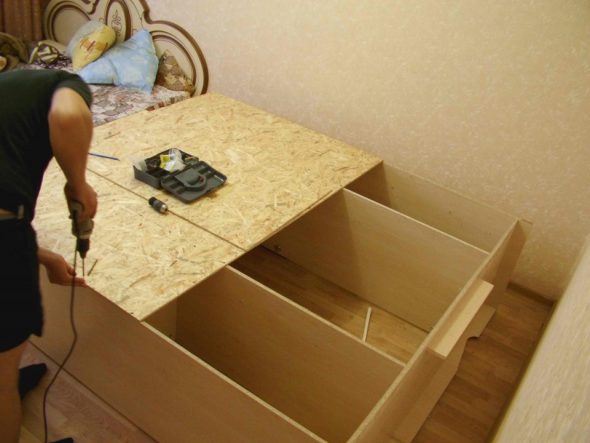
To overcome the problems, you can design a compartment of sections, for
each of which would be enough one sheet.
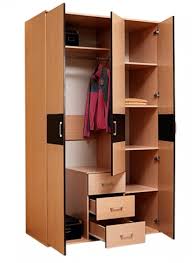
It is best to use screws with washer.
Chipboard is a mixture of sawdust and resin, which under the influence of high temperature and pressure turns into a homogeneous, durable material.
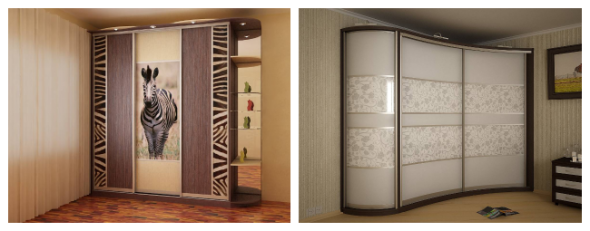
Fixing the back wall of the cabinet is not an idle question.
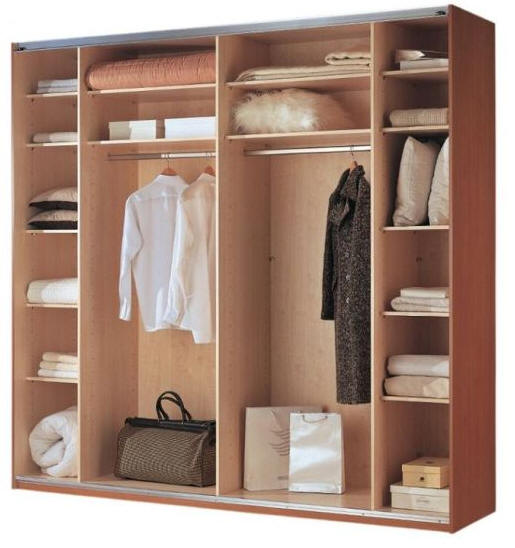
If chipboard is used, the holes are drilled first so as not to
split the slab, and then the screws are screwed.
Differs:
- grades, which are determined by the appearance of the product;
- by the number of layers;
- according to the degree of surface roughness: unpolished,
ground, laminated;
- by density;
- for some other indicators.
Properties | Fiberboard | Chipboard |
Cost of | Low | High |
Thickness
|
3-5 mm
|
10,16,18 mm
|
Influence at
strength constructions |
For tall models not
is recommended
|
Significantly enhances
strength |
Reaction to moisture,
scratch marks
|
One side with a non-laminated surface can absorb moisture, deep scratches can damage the sheet. | Laminated surfaces do not let in moisture, and scratches do not
cause significant material damage |
Diversity
colors
|
Five colors
|
Unlimited
quantity, colors not different from color product body |
The possibility of mounting to the wall of high cabinets | Complicated because of
small thickness slabs
|
Any fixture to the wall |
Parts compatibility | Can only
lay on each friend what can be viewed
|
Tab each other,
organically and seamlessly with parties |
Assembly | Assembly is done in
lying position, which requires additional spaces
|
Cabinet going to
standing position practically in place installations
|
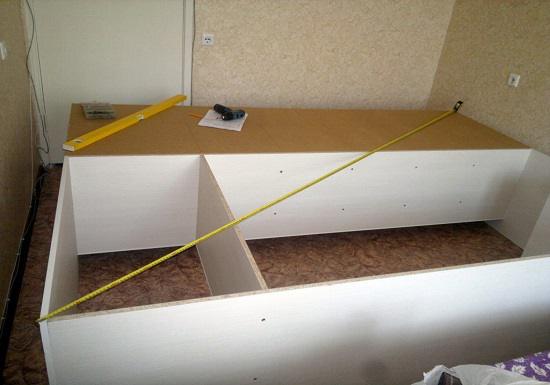
The back wall of the cabinet rigidly fastens the entire structure, keeps it strictly upright.
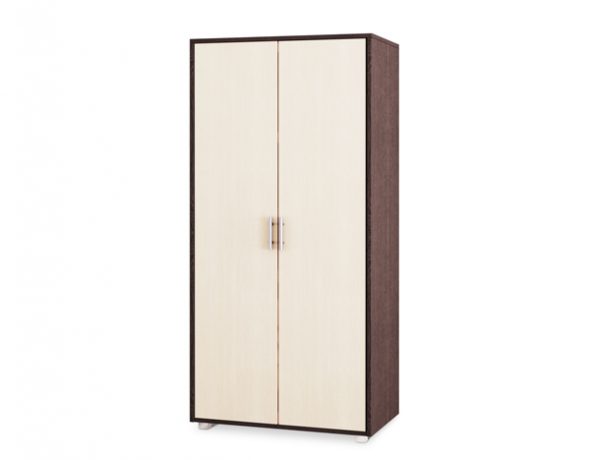
Improves the rigidity of the whole structure and the fastening of the sheets in the grooves selected with a milling cutter in the end posts, lid and bottom of the product.
As we can see from the table, what the back wall of the furniture is made of affects the appearance, ease of assembly, and durability. The back wall of the cabinet, the material of which is laminated chipboard, is better in all respects, but also costs more than five times. Naturally, its use significantly weights the product.
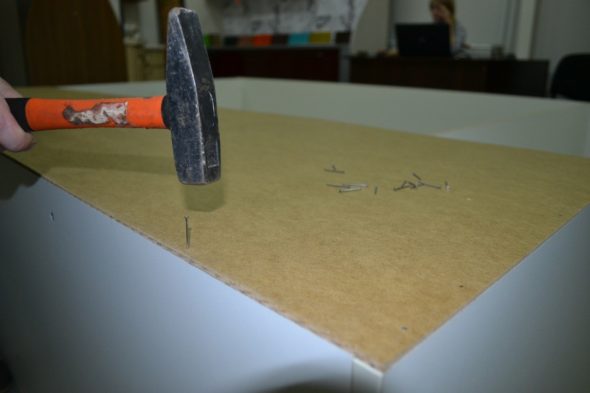
It isolates the interior of the cabinet, making it aesthetic, especially if the wall behind it is uneven, without finishing.
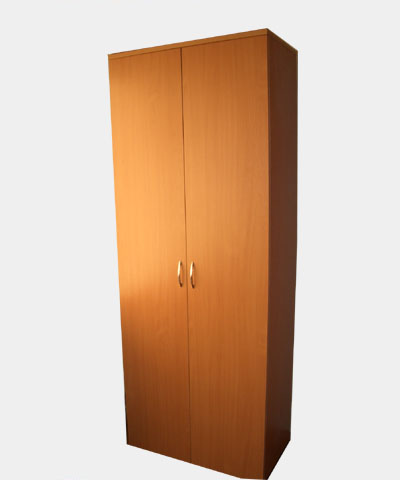
Need to use multiple sheets.
In the case of high-sized models and a large load, for example, in the form of books, the question: from which the back wall of the cabinet should be made, does not arise. For safety and reliability, this should be done from chipboard.
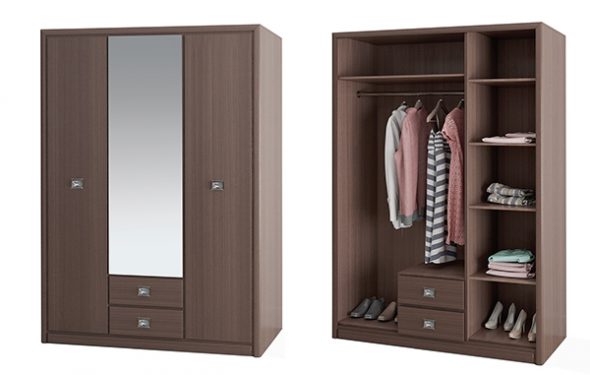
Cabinets can be made as a separate enclosure and built-in.
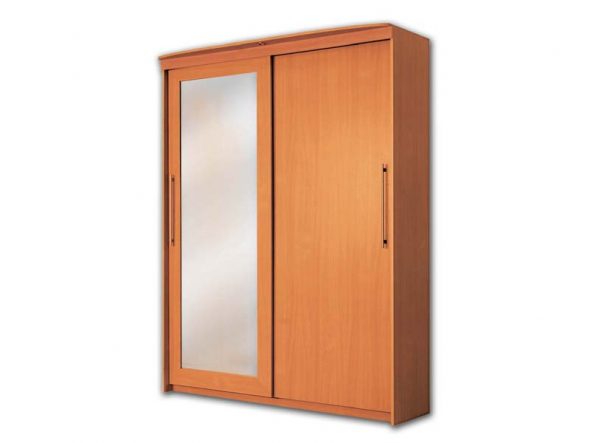
Sections are assembled separately, then they are connected to each other at the place where the product is located further and form a single structure.
In other models, the material of what the back wall of the cabinet is made of can be a fiberboard, which is not only thick and dense. Fiberboard has a good margin of safety. You can also note the duration of operation (up to 30 years) while maintaining the original parameters, the environmental safety of the plates.
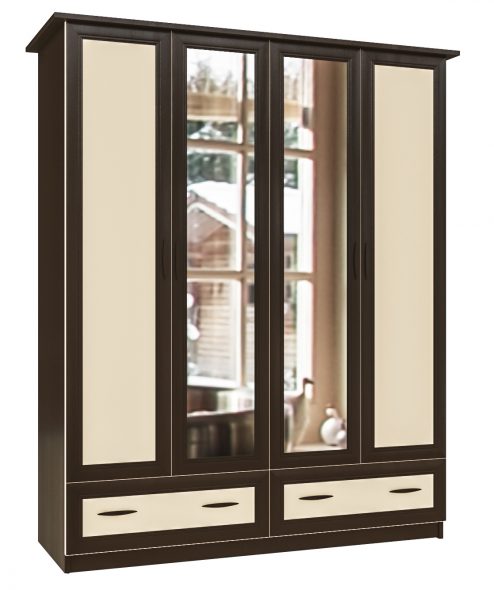
To prevent this, in addition to the rear wall, special stiffening ribs can be provided inside.
How to strengthen the back wall of the cabinet?
Fixing the back wall of the cabinet is not an idle question. Some people suggest nailing the back walls of the cabinets.
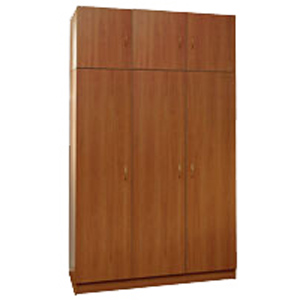
The advantage of individual models is the ability to
to disassemble them, move them and put them in any place.
Yes, this method allows you to do this quickly, but this mounting of the rear walls of cabinets reduces the rigidity of the structure and its strength. In this case, the material of the body and the wall is destroyed, difficulties are created later on when disassembling such a product. Not recommended and the use of construction stapler. It is best to use screws with washer.
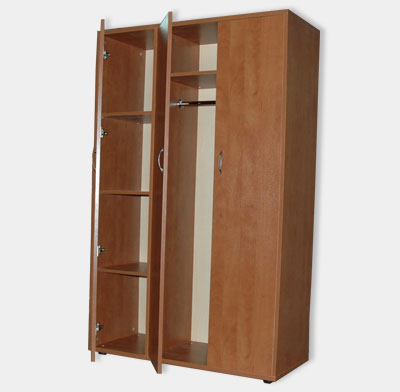
Back wall of the cabinet
the material of which is from chipboard is better in all respects, but it also costs five times more expensive.
If chipboard is used, then the holes are drilled first, so as not to split the plate, and then the screws are screwed. Improves the rigidity of the whole structure and the fastening of the sheets in the grooves selected with a milling cutter in the end posts, lid and bottom of the product. At the same time, it is important that the sizes of the sheet being fixed coincide with the dimensions of the place to be closed.
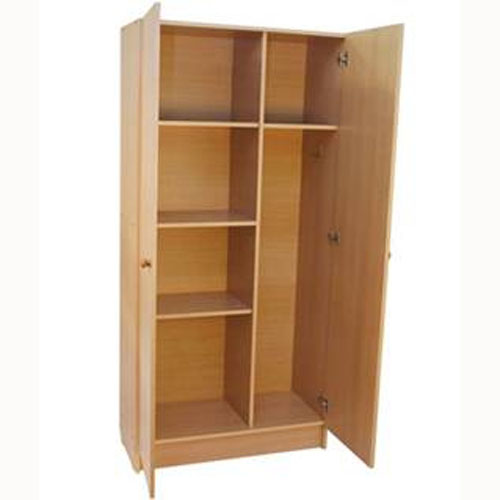
Chipboard is a mixture of sawdust and resin.
Fastening is carried out around the perimeter:
- to partitions and end walls;
- overlap from above;
- to the base of the structure;
- to capitally fixed shelves.
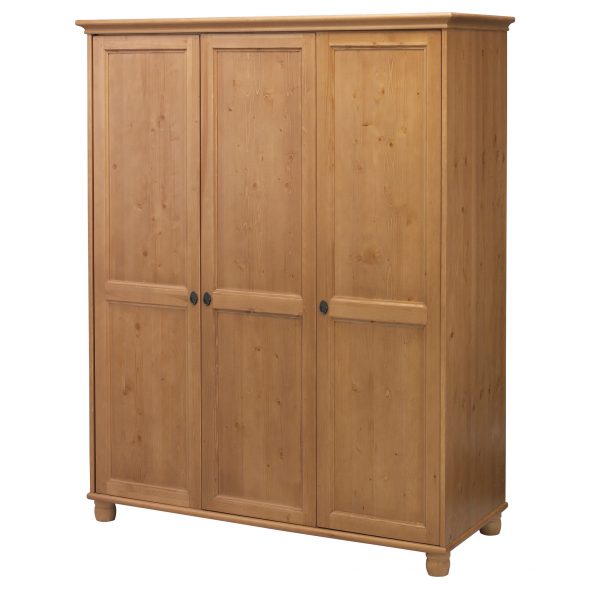
They also differ in the degree of response to moisture, fire resistance, exposure to sunlight.
How to fix the wall at the junction?
One sheet may not be enough to cover the entire back surface. To do this, use a few sheets. In this case, the following sheet joining options are possible:
- if the joint lies on the end of the partition:
- both sheets are pressed against the partition using self-tapping screws and washers;
- sheets overlap;
- if the joint does not fall on the end of the partition:
- both sheets are connected using a mortise bar into which they are inserted;
- sheets are glued together.
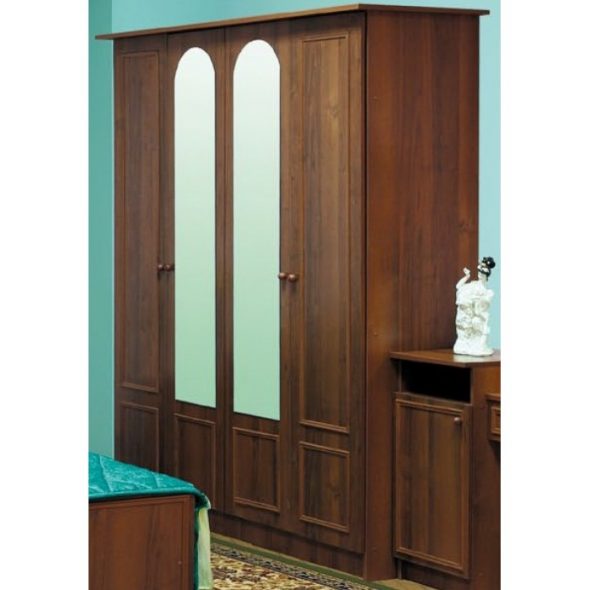
Plates can be smooth on one or both sides, varnished,
covered with laminate film, artificial veneer.
To overcome these problems, you can design a compartment of sections, for each of which would be enough one sheet. Sections are assembled separately, then they are connected to each other at the place where the product is located further and form a single structure.
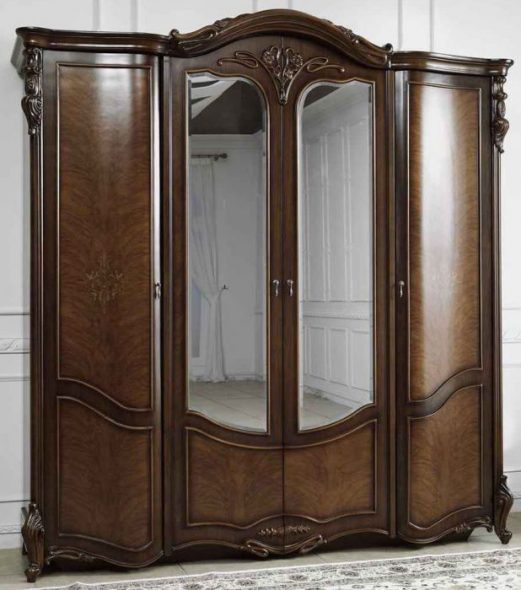
Fiberboard consists of wood fibers, synthetic
resins, fillers, water.
VIDEO:Back wall
50 photo ideas: the back wall of the cabinet
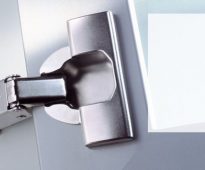
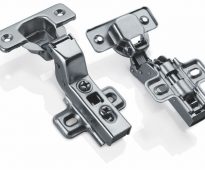
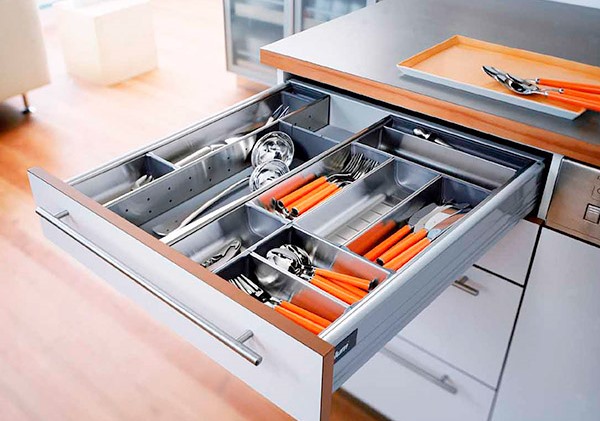
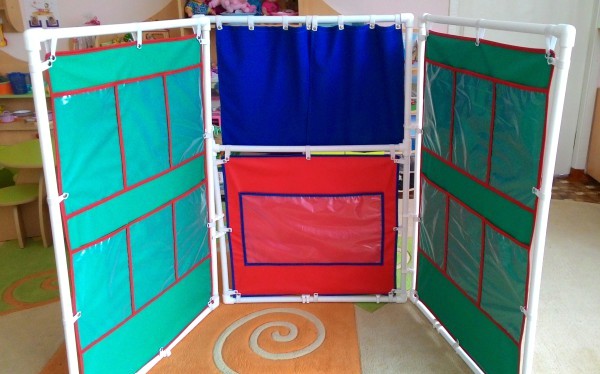