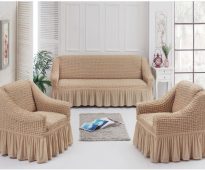
Making a sofa with your own hands
Beautiful sofa is the main design element of any room. This is not just a piece of furniture, but also a business card of the whole house, to which the attention of guests has usually riveted. In specialized stores, such furniture, as a rule, is quite expensive. If you make a sofa with your own hands, it will cost much less. At home, making it is not difficult.
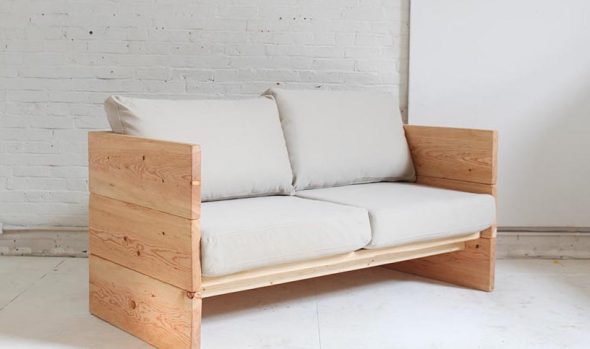
Nowadays, furniture that combines unusual design, style and functionality is becoming increasingly popular.
Content
Independent manufacture of furniture
Using a simple project to make a quality product, even a person who has never worked on the production of upholstered furniture before. If in a modern apartment such a sofa will not look very respectable, then in a country house or in a country house it will fit perfectly into the local interior.
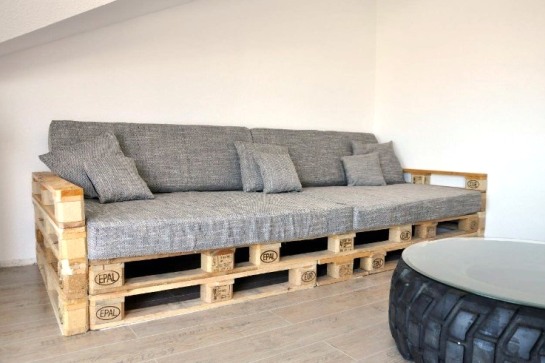
One example is a sofa of pallets with drawers ..
The main components of the product are:
- frame;
- back;
- side parts;
- fabric covering.
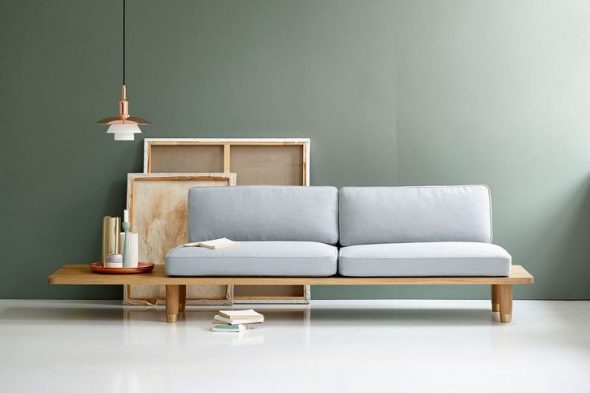
Such furniture can be made independently from scrap materials, giving it the look that you like.
The frame can be of any shape and size. For its manufacture used wooden slats and bars. To make the structure more rigid, apply sheets of plywood or chipboard. Assembly is carried out using a screwdriver. All joints are first lubricated with wood glue, then the wooden parts are tightened with self-tapping screws. In addition, it is desirable to fix the joints with angle metal fasteners.
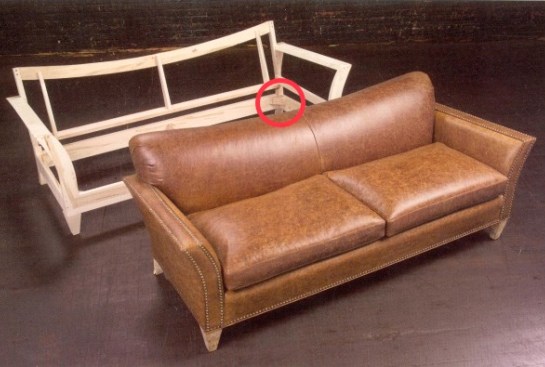
Beautiful sofa is the main design element of any room.
The frame for the mattress is made of boards. To give the product more comfort, the supporting area of the frame can be made of interlaced furniture belts. At first, the belts are mounted vertically on the frame, then horizontal binding is made perpendicularly. In spite of the fact that traditional steel spirals are not used in such a sofa, it will be perfectly springy. Therefore, it will always be nice to lie on it.
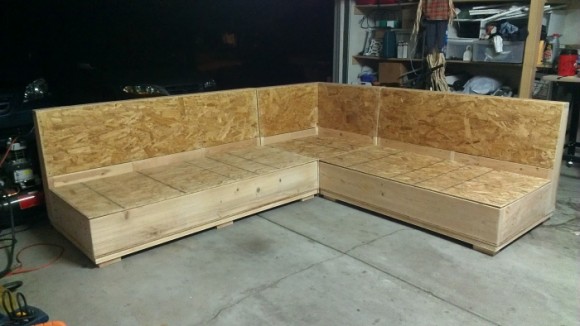
Corner bed looks more prestigious than the usual folding option.
The back is usually made hollow inside. The form can be given it rectangular or sloping. To this end, the end width at the base increases and decreases at the top. The side parts are made in the same way as the back. The top and front side of the back is glued with foam mats. On the inner sides of the side of the foam is glued too. Glue should be applied with a wide brush evenly. Before the glue sets completely, the foam rubber sheets should be pressed tightly against the surface to be glued.
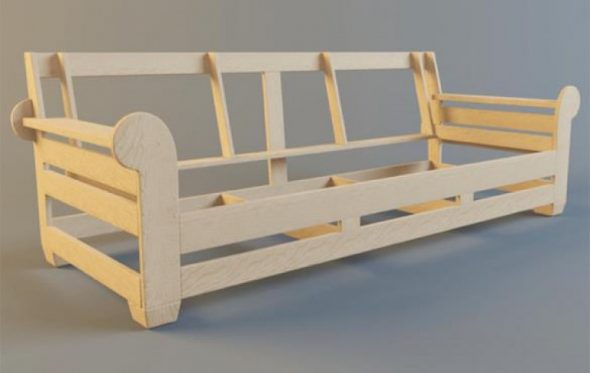
Independent production of household goods makes it possible to create an original design that fits perfectly with the interior of a particular room.
The fabric covering is carried out on the prepared patterns or patterns. If you do not have them, they are easy to do yourself. For this, a fabric is applied to each element of the sofa, after which the necessary cuts are made.After covering all the components of the fabric, the final assembly. The simple design of such furniture is usually performed in three days.
For the manufacture of a rounded sofa most often used furniture panels. They are made from wood or thick plywood. Such material allows round design to cope with the required load. To secure the upholstery in the dimensions of the individual parts must be a certain stock. The lower soft parts under the skin should be made multi-layered. Due to this, it will be much softer and more comfortable to sit.
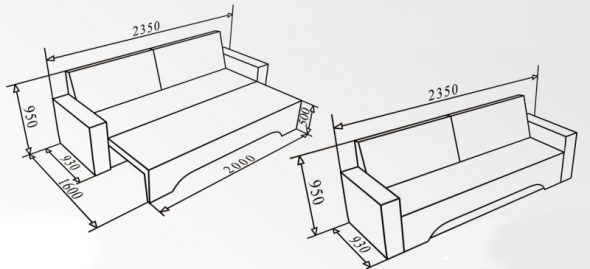
To begin the manufacture of a sofa-book follows with the creation of separate frame elements of the whole structure.
How to make a sofa book
To begin the manufacture of a sofa-book follows with the creation of separate frame elements of the whole structure. This includes the sidewalls, back, seat, box for linen. First, the linen compartment is made of boards. This frame is reinforced at the corners with short pieces of bars, and is supplemented with rails from below. For the back and the seat is also used bars, which are connected by screws or special nails with a notch.
At production of a sofa such tool is used:
- hacksaw for wood;
- screwdriver;
- plane;
- hammer;
- scissors.
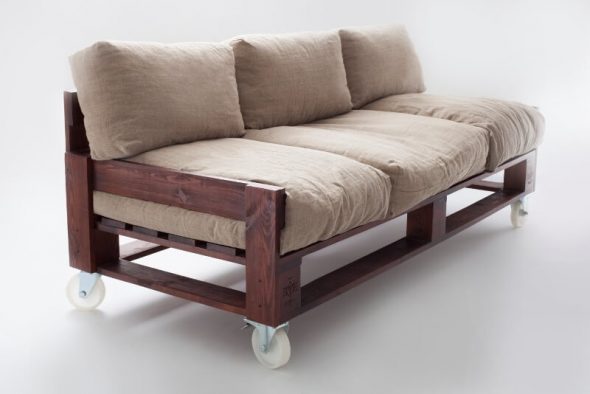
For the back and the seat is also used bars, which are connected by screws or special nails with a notch.
To the received frames screw wooden lamellae. They should play the role of support for the mattress. After all the frames are ready, the assembly is made. However, special mechanisms are needed. You can buy them in the construction market or in the store. During the installation of mechanisms between the folding parts need to leave a gap of approximately one centimeter.
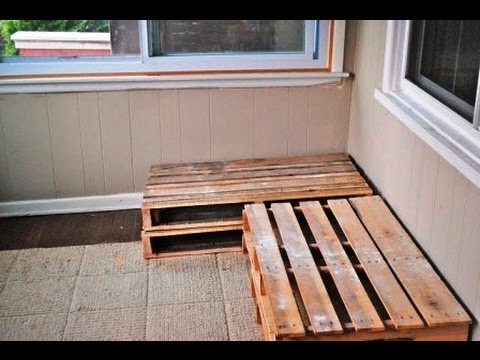
The quality and comfort of sitting on the sofa will depend on the quality of this element.
In this case, the sofa should be decomposed. Due to the presence of the gap, it will be free to fold and unfold. Before laying the foam rubber, you must first glue interlining on top of the lamellae. This will allow portions of foam sheets between the lamellae not to fall. The surface will always remain flat. So that the sheets do not interfere with the folding mechanisms, the corners near these parts are cut off.
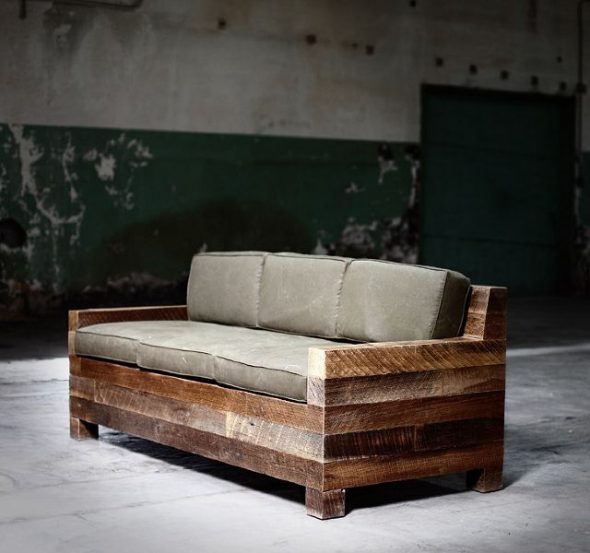
However, special mechanisms are needed.
A soft cushion is usually made on the edge of the seat. For this, an additional foam strip is glued on top of the continuous layer. The lower edge of the strip is bent under the seat and also glued. The armrests are softened in the same way. A similar procedure is performed with the back. When the glue under the foam completely dries, covers are sewn to the size of the furniture.
Making a corner sofa
First, the bottom is done, that is, the seat. The joined boards are fastened with screws and corner plates. Chipboard sheets are screwed to the bottom box. For support is a separate frame. The support part is also covered with plywood. Behind you can pull the dense matter. Product dimensions are associated with the parameters and shape of the mattress.

During the installation of mechanisms between the folding parts need to leave a gap of approximately one centimeter.
The stages of manufacturing additional design are similar. To connect the individual parts, the corner structure is made. Usually it is made of the same material as the main elements. During the manufacture of this design should consider the angle of rotation. The back and supporting parts are pasted over with batting. The back side is covered with a thick cotton fabric.
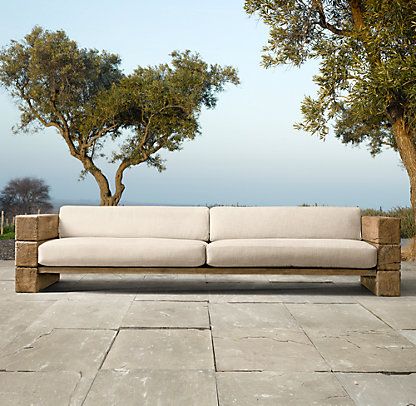
Family members spend a lot of time on it.
The legs are usually made from square pieces of timber. Holes are drilled for attachment to the lower frame in the bars. After that, they are applied to the bottom of the frame and fastened with long screws.In the manufacture of such furniture should pay special attention to the design of the structure. If it is not done correctly, various deflections and deformations may appear in the future, as well as other similar defects.
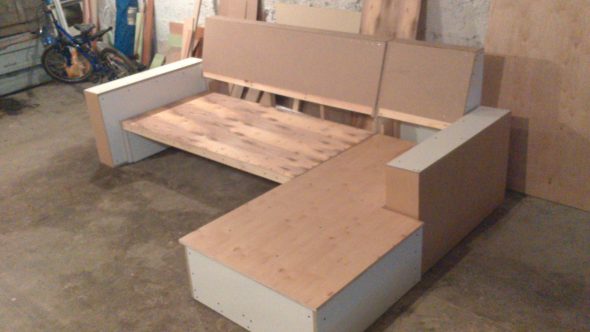
Behind you can pull the dense matter.
For the manufacture of furniture are used such materials:
- board;
- timber;
- foam rubber;
- DSP;
- furniture fabric;
- carpenter's glue.
If in the furniture salon you decide to buy some unusual bed, then it may not be affordable for you. Original products are very expensive. It will be much better to make a custom sofa bed with your own hands. It requires bars, boards and sheets of plywood of appropriate thickness. The back gathers from levels and pieces of a bar. The front part of the assembled frame is best to sheathe sheets of chipboard.
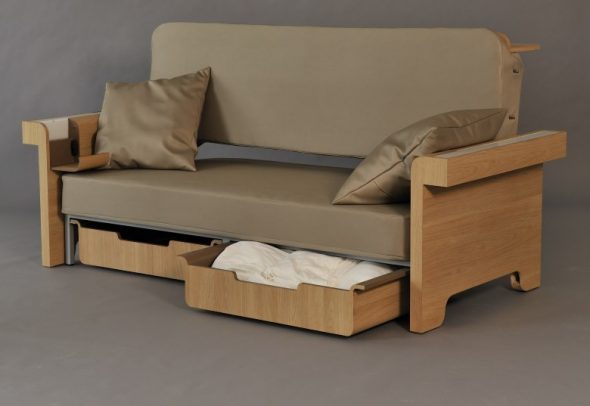
The stages of manufacturing additional design are similar.
They are quite durable, and in stores building materials are inexpensive. It is advisable to process the collected base with a stain or varnish. Because of this, it will last much longer. Foam sheets are used for soft parts of the product. Fabric materials are attached to the frame with special nails with wide caps.
Unusual sofas
Often they are made of improvised material. Especially if the product is intended to give. The basis and a back of this furniture can be made of the used shutters of doors. Details are cleaned from the old coating and dirt, and then treated with a grinding machine. Then they need to paint or glue the veneer. One door leaf is installed on wooden supports. The second flap is used as a back. It should be attached to the base at a convenient angle.
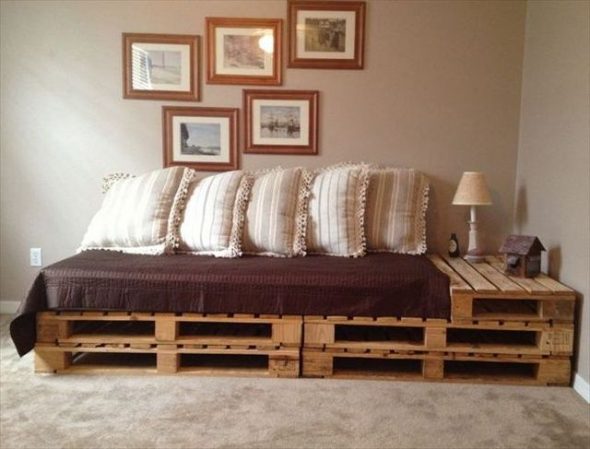
In the cozy home is always beautiful furniture.
The mattress is cut from foam rubber. A piece of material must match the size of the seat. The received preparation at first is covered with dense fabric, then from above the beautiful fabric having good quality is put on. In the manufacture of such furniture should pay special attention to the reliability of the frame basis. It should easily withstand the load that arises from sitting on the couch of several people.
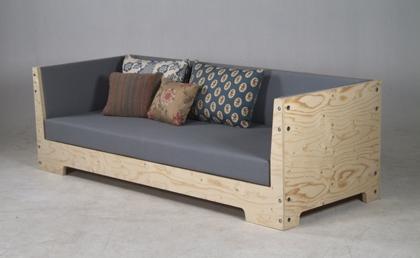
Often they are made of improvised material.
Beautiful and cozy furniture for rest can be made with drawers in which it is convenient to store bedding and clothing. Due to the high functionality of the design, in the bedroom there will be no need to install an additional dresser or wardrobe. This will save living space, make the room more spacious.
The product includes the following components:
- back;
- seat;
- a pair of armrests;
- drawers.
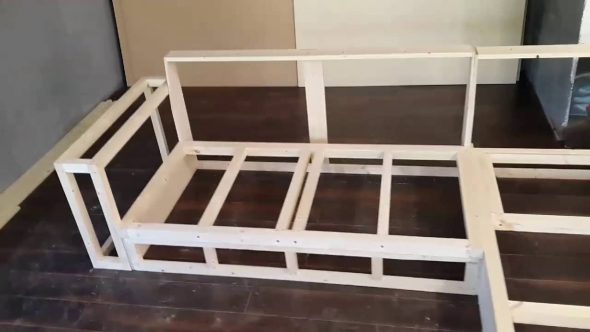
He must easily withstand the load that arises from sitting on the couch of several people.
Each part of the product is knocked down separately. The back gathers from long levels. To provide the necessary rigidity, the planks are reinforced with short transverse bars. To get a sloping back, the back plates must be longer and the front ones shorter. Chipboard sheets are installed on top of the received frame, which are then pasted over with foam rubber and sheathed with fabric.
For the seat is mounted a similar frame. Its only difference is that it does not have a beveled part. On the sides are attached armrests. They should be fastened with long screws in several places. Drawers are made frameless. The material here is also used chipboard. To make both drawers easily extendable, special mechanisms are installed on the frame posts.
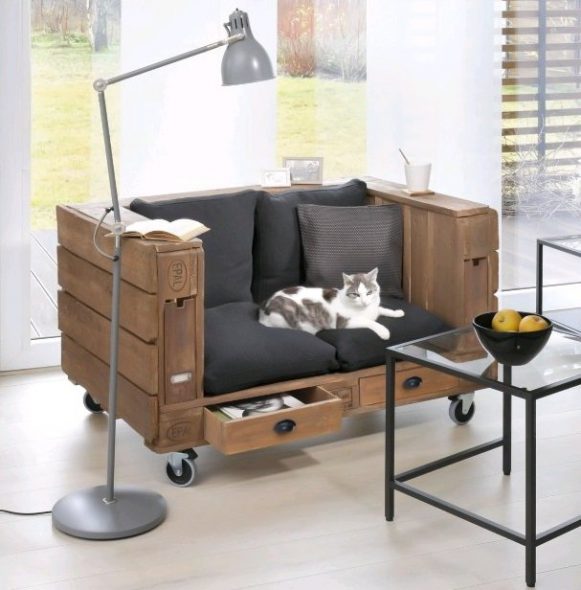
Beautiful and cozy furniture for rest can be made with drawers in which it is convenient to store bedding and clothing.
After all the details are covered with foam rubber, the padding polyester is laid on top of it. Further to protect the soft material, the entire sofa is sheathed with a sturdy cloth.The quality of the final plating depends on the appearance of the furniture. If you want your product to look fashionable and respectable, you can use leather or a good leatherette. Now in the construction markets of such materials are a large number.
The use of scrap materials
From simple elements you can make furniture that will easily fit into any interior. If the design consists of natural wood, the product will regularly serve more than one year. Worn covers or fabric lining, if necessary, is easy to replace. Today, those pieces of furniture that have an unusual design and style are popular. By making goods from scrap materials, you can give it the most unexpected, exclusive look.

Each part of the product is knocked down separately.
Independent production of household goods makes it possible to create an original design that fits perfectly with the interior of a particular room. If your own product turned out to be fashionable, reliable and beautiful, you can be proud of it, show off to your friends. Creating your own furniture sets can be done by anyone who knows at least a little how to use carpentry tools and has patience. To create an original furniture masterpiece, it is enough to turn on the fantasy, to show a little bit of perseverance and hard work.
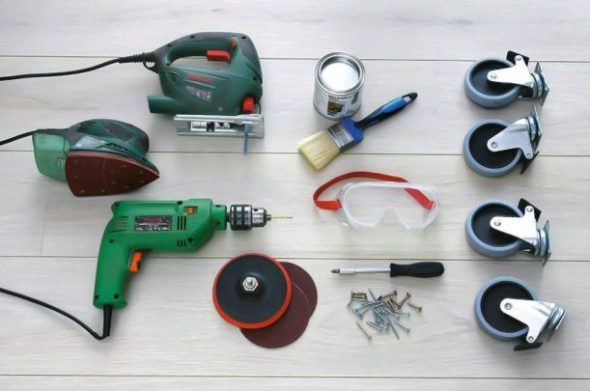
Chipboard sheets are installed on top of the received frame, which are then pasted over with foam rubber and sheathed with fabric.
In the cozy home is always beautiful furniture. The main place, as a rule, takes a luxurious sofa. Family members spend a lot of time on it. Here they play with children, sleep, arrange gatherings with close friends. Before producing your own sofa, you need to be well aware of the type that will best suit the needs of all family members.
The most popular products are:
- corner;
- book;
- dolphin;
- with folding mechanisms.
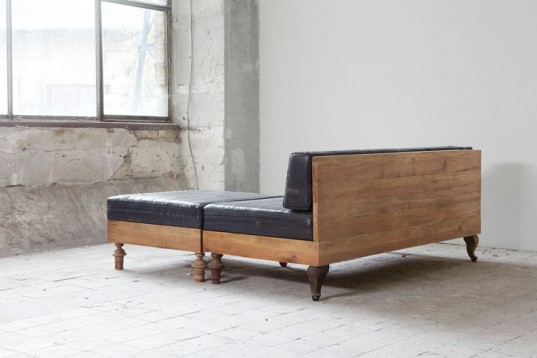
For the seat is mounted the same frame
This also includes an ottoman. Such a product is extremely simple. It lacks any folding mechanisms. Therefore, it is not difficult to make an ottoman with your own hands. It is desirable to choose a future bed, taking into account the place where it will be installed. Before you begin, you should take the necessary measurements, make preliminary drawings.
Joinery Rules
Corner bed looks more prestigious than the usual folding option. If you are doing this work for the first time, it is better to make the simplest crafts that do not have any additional shelves and drawers. When assembling the frame, do not try to make spike joints at the ends of the boards. Such work is performed only by professional carpenters. It is not desirable to fasten separate elements with nails. As the assembly is constantly loosened, over time the nails begin to loosen the fastener. It is better to use screws or screws.
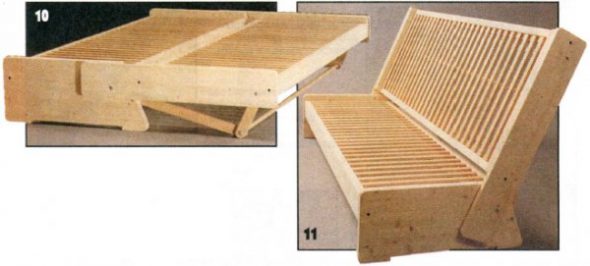
Now in the construction markets of such materials are a large number.
From natural wood should give preference to conifers. Their fibrous structure is saturated with resin, which protects the tree from rotting processes. Due to this, pine products have a rather long service life. Before starting the assembly, finished elements must be carefully polished. This will provide the necessary security for future work. Cutting materials is desirable to carry out on the street, since this produces a large amount of wood dust.
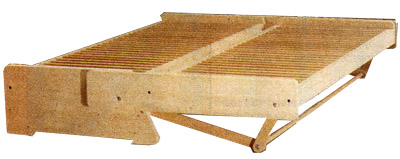
From simple elements you can make furniture that will easily fit into any interior.
Rama is the main part. All other parts are attached to it. When assembling the seat, you need to check the box for matching diagonal sizes. The correct form of the box ensures the stability of the entire frame. Before attaching the casing, check all connections.If any joint reeling, it should be reinforced with additional screws or metal corners.
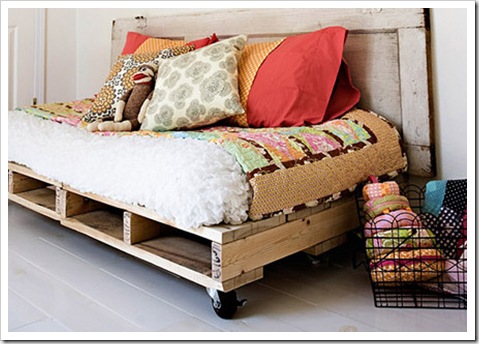
By making goods from scrap materials, you can give it the most unexpected, exclusive look.
Further measurement is taken from all surfaces. According to the obtained dimensions, individual elements are cut out of foam rubber, which are then glued. All soft parts should fit tightly together. Foam rubber for the seat should be much thicker than for the back. If you do not have a thick layer, you can glue together several separate layers of thin material. The quality and comfort of sitting on the sofa will depend on the quality of this element.
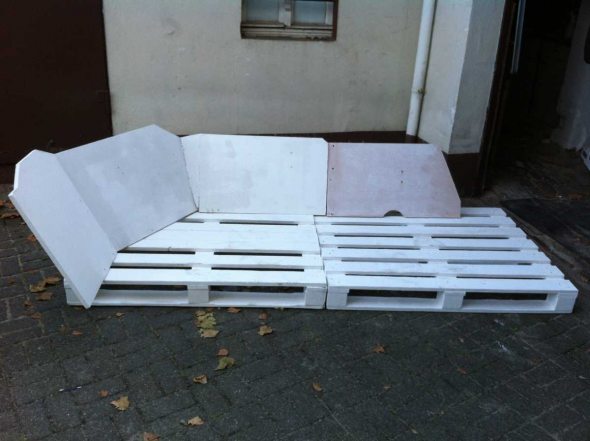
Independent production of household goods makes it possible to create an original design that fits perfectly with the interior of a particular room.
VIDEO: Do it yourself furniture. Making a sofa. Part 1 Frame.
50 photo ideas how to make a sofa with your own hands
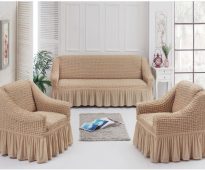
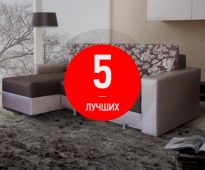
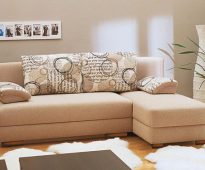
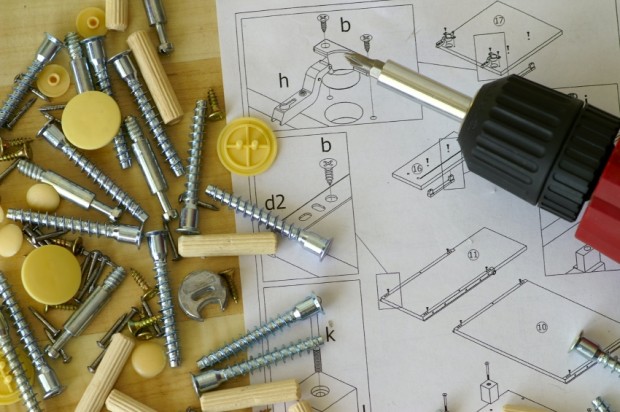
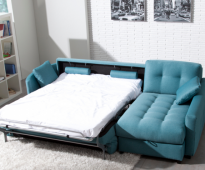
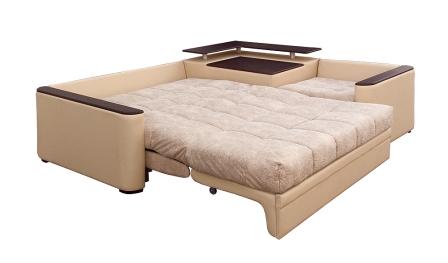